Today's dynamic marketplace has pushed businesses to put maintenance management at the forefront of their operational strategy. Smart organizations now understand that proper maintenance oversight directly impacts their bottom line and operational efficiency. While installing a Computerized Maintenance Management System (CMMS) marks a crucial step forward, true success demands more than just new technology. Organizations must approach CMMS adoption as a comprehensive initiative requiring thorough preparation, precise deployment, and continuous refinement to achieve optimal results.
When properly executed, CMMS deployment revolutionizes maintenance practices, helping teams move beyond constant emergency repairs toward data-backed preventive strategies. This evolution typically yields impressive results across essential metrics - equipment reliability improves, maintenance expenses drop, downtime decreases, and workplace safety standards rise. However, before diving into implementation, decision-makers should thoroughly evaluate both CMMS technology and its potential organizational impact.
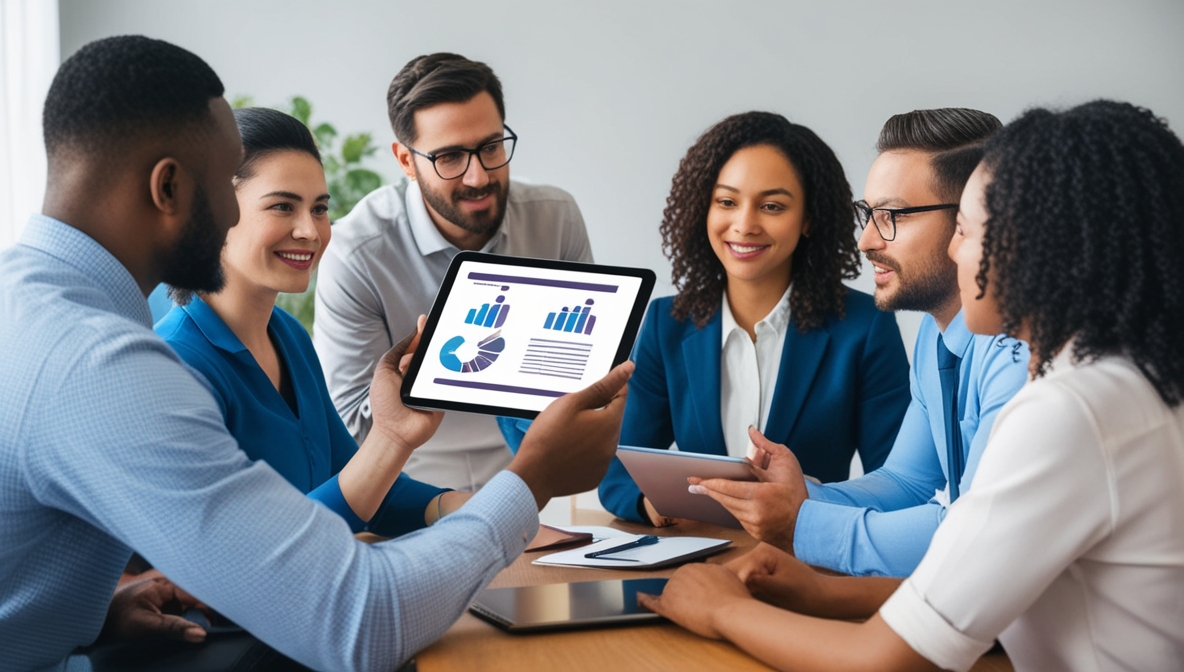
Getting to Know CMMS: Core Functions and Value
What Makes CMMS Different?
At its core, a Computerized Maintenance Management System represents the next evolution in maintenance oversight. This specialized platform consolidates asset management, work order processing, preventive maintenance scheduling, parts inventory, and performance analytics into one cohesive system. It effectively replaces traditional manual record-keeping methods, offering maintenance teams unprecedented control and insight into their daily operations.
The Strategic Value of CMMS Implementation
In an era where operational excellence determines market success, companies face mounting pressure to trim costs while boosting productivity and asset performance. Given that maintenance often represents a major operational expense, poorly managed upkeep can trigger expensive breakdowns, production delays, and safety concerns. CMMS implementation directly addresses these challenges.
Through strategic CMMS deployment, organizations can streamline maintenance workflows, better utilize their resources, and leverage real-world data to enhance their maintenance program's effectiveness while reducing unnecessary spending.
Key Advantages of Successful CMMS Adoption
Organizations that properly implement CMMS solutions typically realize multiple benefits:
- Minimized Equipment Downtime: Strategic maintenance scheduling and efficient work order systems help maximize operational continuity
- Reduced Maintenance Expenses: Enhanced efficiency combined with smarter resource allocation delivers measurable cost reductions
- Extended Equipment Life: Consistent preventive maintenance helps assets perform optimally for longer periods
- Stronger Safety Performance: Systematic tracking of safety protocols and hazard assessments promotes a safer workplace
- Optimized Parts Management: Advanced inventory tracking capabilities ensure critical parts availability while minimizing excess stock
- Evidence-Based Planning: Rich maintenance data enables informed choices about resource deployment, maintenance tactics, and equipment replacement timing
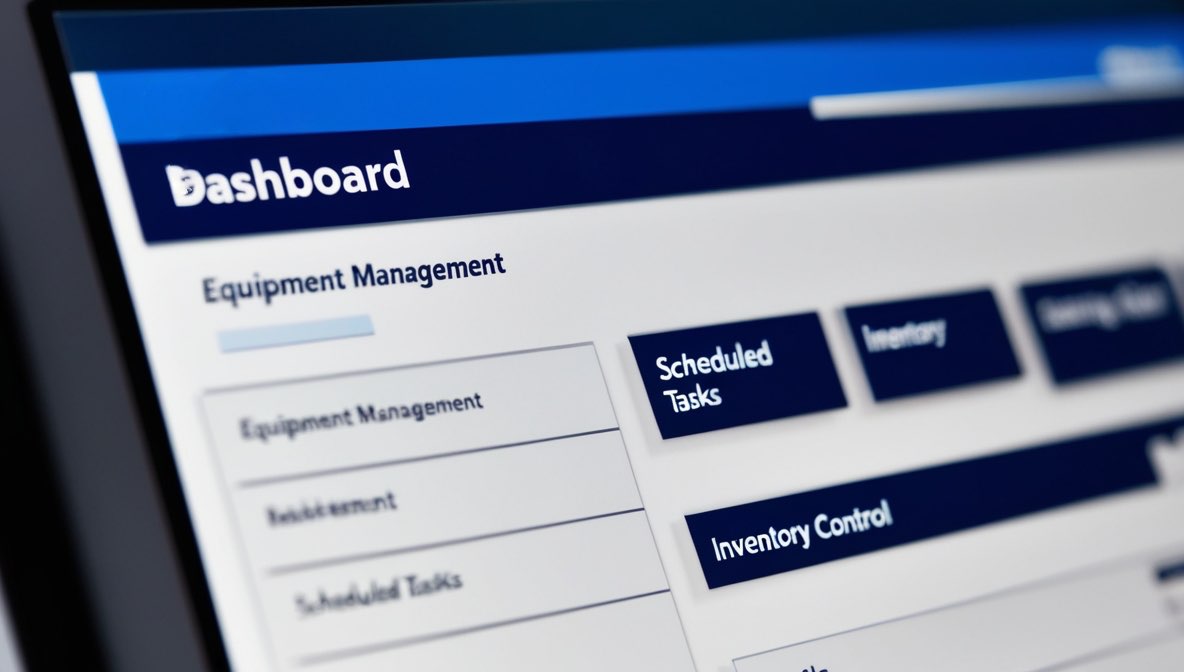
Selecting Your Ideal CMMS Solution
Key Selection Criteria
Finding the perfect CMMS match requires careful evaluation of your organization's unique needs. The success of your maintenance management overhaul largely depends on choosing appropriate software. Let's explore the crucial aspects to consider during your selection process.
Real-World Cost Considerations
Last month, I spoke with a plant supervisor from Michigan who learned an expensive lesson. Their supposedly cost-effective CMMS solution came with unexpected expenses at every turn. Basic training sessions required additional payments. Moving their existing data cost extra. Even pulling specialized reports meant paying more. It reminded me of those deceptively cheap printers that drain your wallet through endless ink purchases.
Meeting Industry-Specific Demands
Every sector faces distinct maintenance challenges. Manufacturing facilities typically need robust preventive maintenance and work order systems to keep production flowing smoothly. Meanwhile, healthcare organizations often prioritize detailed asset tracking and compliance features to maintain patient care standards. Your chosen CMMS must align with your industry's particular requirements.
Matching Company Scale and Structure
Your organization's dimensions and complexity should guide your CMMS choice. Smaller operations might benefit from straightforward cloud solutions offering core functions and easy setup. Larger corporations spanning multiple sites typically require sophisticated on-site systems with advanced features like multi-location coordination and detailed analytics. Understanding your organizational structure helps narrow down suitable options.
System Compatibility Considerations
Evaluate how well potential CMMS solutions work with your current business systems, from ERP to inventory platforms. Smooth integration enables better data flow and streamlined processes. For instance, connecting your CMMS with inventory systems can trigger automatic parts orders when supplies run low, preventing repair delays. Carefully assess how each CMMS option fits within your existing technology framework.
Focus on User Experience
Your chosen CMMS should feel approachable and accessible to everyone who needs it, regardless of their tech comfort level. Features like clear interfaces, mobile access, and customizable views encourage widespread adoption. This matters especially for maintenance staff who may be transitioning from manual systems. An intuitive CMMS drives better engagement and results.
Provider Credibility and Service
Invest time researching CMMS vendors' market performance. Look for companies demonstrating implementation success, responsive support teams, and continuous product improvement. Gather insights through online feedback, industry events, and conversations with current users. Partnering with a reputable provider significantly impacts your long-term maintenance management success.
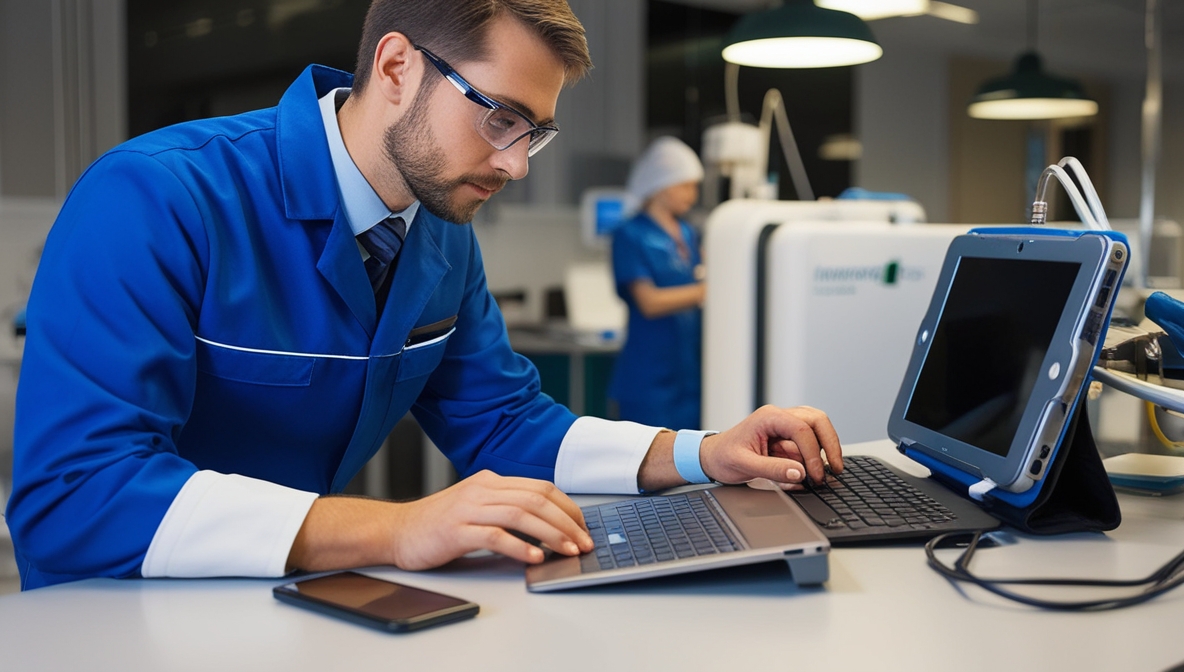
Understanding CMMS Options: Main System Categories
CMMS platforms generally fall into two deployment approaches:
- Cloud Solutions: These systems run on vendor infrastructure and connect through web browsers. Benefits include minimal startup investment, quick deployment, automatic upgrades, and remote access capabilities. Small businesses or those with limited tech support often prefer this route.
- Local Installation: These versions install directly on company servers under internal IT management. While offering enhanced security control and customization freedom, they need bigger initial investment and dedicated tech support. Large enterprises or organizations with strict data protocols typically choose this option.
Essential System Capabilities
When reviewing CMMS options, prioritize these core functions:
- Task Assignment Tools: Efficient systems for generating, distributing, monitoring, and completing maintenance tasks.
- Planned Maintenance Tools: Features enabling maintenance scheduling based on timeframes, equipment usage patterns, or performance indicators.
- Equipment Oversight: Tools tracking machine details, repair records, warranty information, and related documentation.
- Parts Control: Functions managing replacement parts, including stock monitoring, reorder triggers, and purchase management.
- Performance Tracking: Comprehensive analysis tools providing maintenance metrics, cost data, and trend information.
- Field Access: Mobile device compatibility letting technicians update records while working onsite.
Choosing Your CMMS Partner
Selecting the right provider matters as much as picking appropriate software. Evaluate potential partners using these criteria:
- Industry Knowledge: Search for companies with solid implementation success in your business sector.
- Technical Assistance: Review their support structure, including response efficiency, availability windows, and help resources.
- Development Vision: Examine their upgrade plans and commitment to continuous platform improvement.
- Cost Structure: Analyze pricing models to ensure they match your financial plans and organizational requirements.
- Setup Support: Investigate their implementation assistance, including staff training, data transfer help, and ongoing guidance.
Consider requesting trial access or detailed demonstrations to properly evaluate system usability before making your final choice.
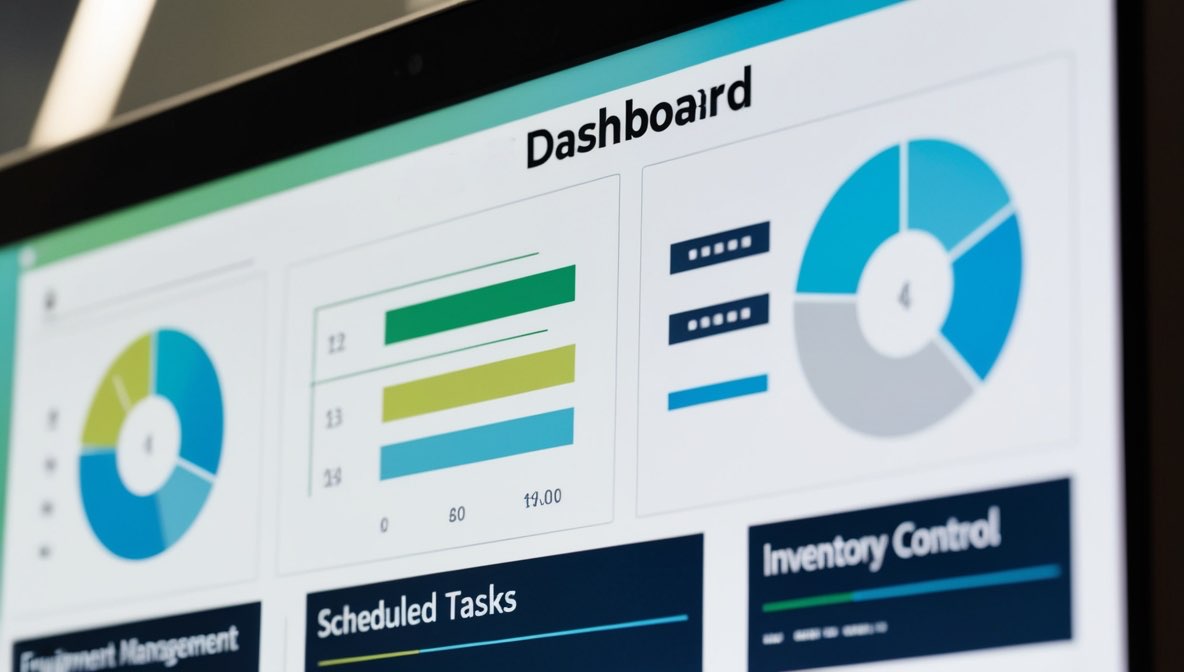
Creating an Effective CMMS Implementation Strategy
Strategic Planning Significance
A detailed implementation roadmap proves essential for CMMS project success. Projects lacking thorough planning often face timeline slips, budget overages, and staff resistance. Comprehensive preparation aligns team expectations, maximizes resource usage, and keeps initiatives running smoothly.
Many organizations learn this lesson the hard way - rushing into CMMS deployment without proper groundwork typically leads to unexpected hurdles, missed deadlines, and systems that fall short of business requirements.
Implementation Process Framework
While specific steps vary by organization and chosen platform, consider these core implementation guidelines:
- Set Clear Targets: Establish concrete objectives for your CMMS initiative. What improvements do you seek? Common goals include cutting equipment downtime, reducing maintenance expenses, boosting asset performance, and strengthening safety protocols.
- Build Your Project Team: Create a dedicated group drawing members from maintenance, technology, operations, and financial departments. Designate a project leader to guide progress and maintain momentum.
- Review Data Quality: Evaluate your current maintenance records for accuracy, completion, and uniformity. This reveals potential data cleanup needs before system migration begins.
- Customize Platform Settings: Partner with your vendor to tailor the system to your operations. This covers user permission setup, process flows, reporting tools, and existing system connections.
- Design Training Strategy: Create role-specific learning programs for all system users. Consider mixing online modules, classroom sessions, and hands-on practice for optimal results.
- Perform System Checks: Run thorough testing before launch to verify functionality meets requirements. Consider having key users conduct acceptance testing to validate system performance.
- Execute Launch Plan: Develop detailed transition steps for system activation. Choose between gradual implementation across departments or full organizational rollout based on your needs.
- Evaluate Results: Schedule a thorough review several months post-launch to measure system impact and identify potential improvements.
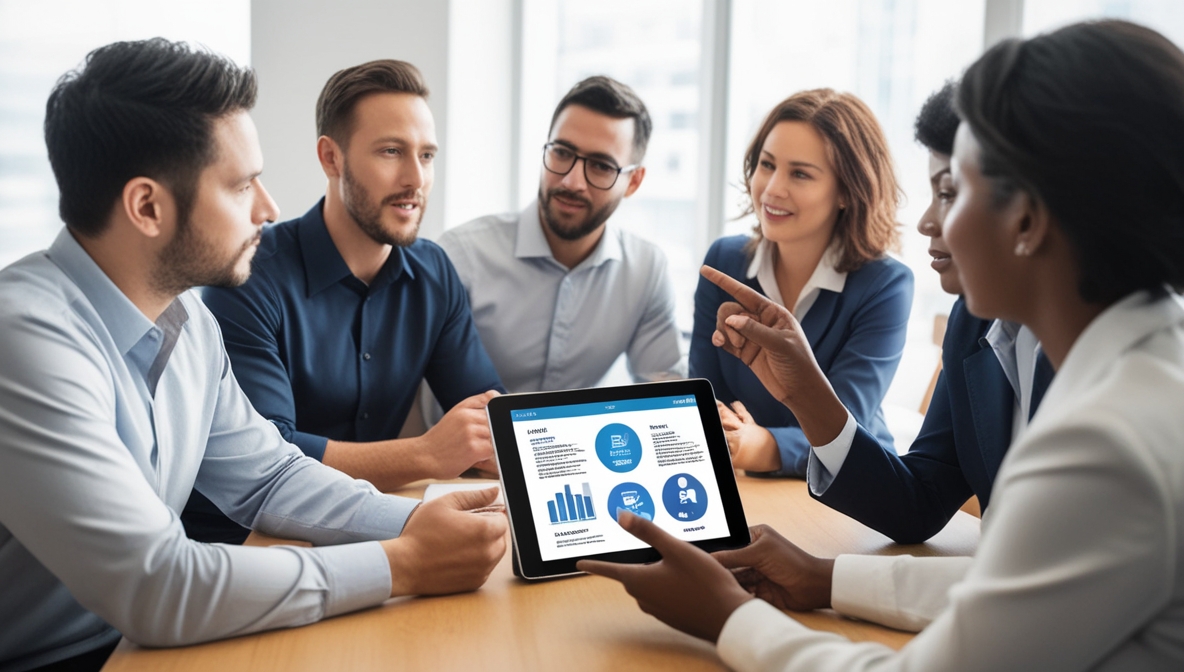
CMMS Data Transfer Guide
Introduction to Data Transfer
Moving your maintenance records from existing platforms into a new CMMS represents a vital implementation phase. This step preserves your valuable maintenance history while setting up your assets for future tracking.
Common Transfer Hurdles
The data transfer process often presents several key challenges:
- Record Variations: Legacy systems frequently contain mixed formats, naming standards, and detail levels across entries.
- Missing Information: Older records might lack critical details, from maintenance histories to equipment specifications.
- Transfer Risks: Moving large amounts of data always carries potential loss risks, demanding careful backup planning.
Proven Transfer Strategies
Follow these tested approaches to ensure smooth data migration:
- Data Cleanup: Start with thorough record review and standardization. Focus on unifying naming systems, eliminating duplicates, and fixing inaccuracies. Remember - investing time in proper data organization now pays dividends in system effectiveness later.
- Field Alignment: Create detailed plans showing how information from your current system will map to new CMMS categories. This ensures proper data placement and maintains information integrity.
- Accuracy Checks: After moving records, verify everything transferred correctly. Compare reports between systems, run detailed audits, and check random entries for completeness.
Through careful planning and execution of these steps, you'll build a solid foundation for your new maintenance management system.
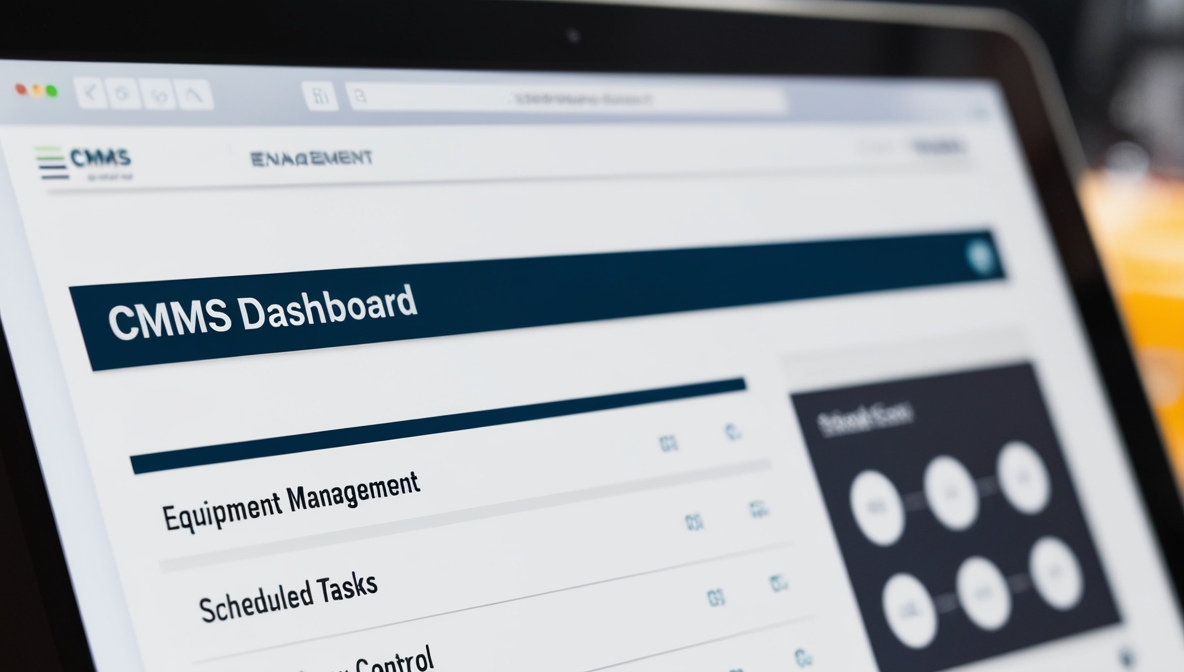
Launch Strategy and System Activation
After completing data transfer, configure your CMMS to match organizational workflows. This includes establishing access levels, designing maintenance procedures, building custom report templates, and connecting to your existing business software like ERP or inventory systems.
User Testing Phase
Thorough testing remains crucial before full deployment. Select representative staff members to operate the system under real conditions, verifying it meets daily operational needs. This testing phase helps spot potential issues requiring attention before organization-wide release.
Deployment Options
Organizations typically choose between two main launch approaches:
- Gradual Implementation: Launch the system incrementally, beginning with selected departments or user groups. This method allows controlled testing and refinement before expanding coverage. Your team can address challenges on a smaller scale first.
- Complete Rollout: Activate the system across all departments simultaneously. While offering faster implementation, this approach requires careful planning since any problems affect everyone at once.
Choose your approach based on your organization's specific requirements and risk tolerance.
Ongoing Launch Support
Maintain strong user support after system activation to ensure smooth adoption. Consider establishing:
- Technical assistance teams
- Digital learning resources
- Internal CMMS experts who can guide colleagues
This support structure helps users navigate the transition period effectively and maximizes system benefits.
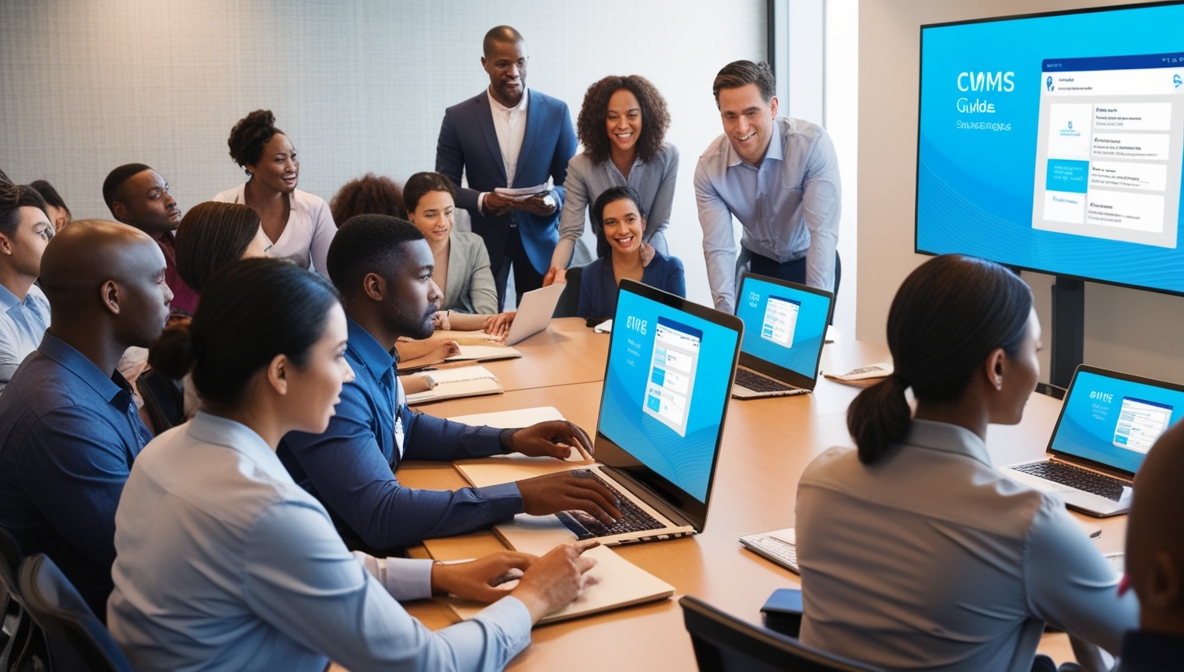
Training and User Engagement
Quality CMMS instruction plays a vital role in system success. Inadequate training often leads to user reluctance, underutilized features, and diminished returns on your technology investment. Well-trained teams use the system confidently and effectively.
Learning Approaches
Organizations can utilize several training methods:
- Digital Learning: Self-paced online modules offer flexible, cost-effective training for large teams.
- Group Sessions: Traditional classroom settings enable direct instructor interaction and peer learning opportunities.
- Practical Application: Hands-on practice using real workplace scenarios helps reinforce system knowledge.
Select training methods that align with your team's learning preferences and operational needs.
Adoption Enhancement Methods
Beyond basic training, consider these proven strategies to boost system acceptance:
- Staff Participation: Include end users in platform selection and setup decisions. Their input creates personal investment in system success.
- Value Communication: Show teams how CMMS tools simplify their daily tasks while supporting broader organizational goals.
- Continuous Assistance: Maintain readily available help resources long after initial training ends.
- Success Recognition: Acknowledge early system champions and share positive outcomes to encourage wider adoption.
These approaches help integrate CMMS firmly into your maintenance culture while promoting ongoing operational improvements.
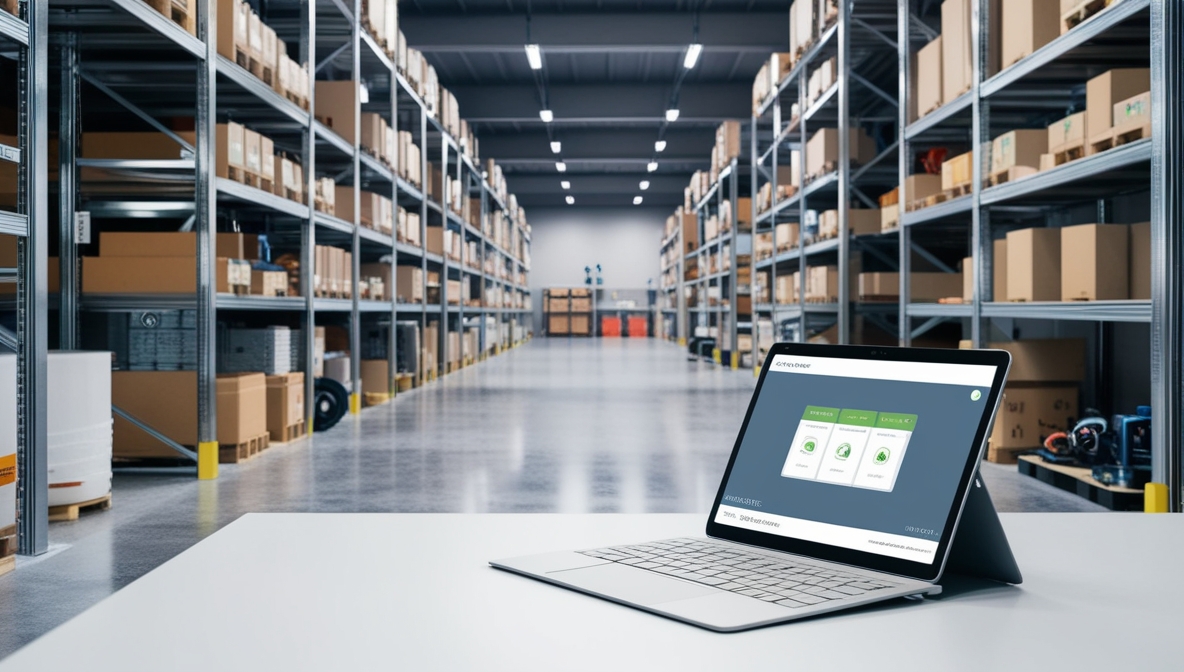
CMMS Performance Refinement
Successful CMMS deployment extends beyond initial setup - it requires continuous evaluation and improvement. After users master basic functions, focus shifts to maximizing system effectiveness and achieving maintenance objectives.
Priority Improvement Areas
Several aspects deserve attention for optimization:
Cost Management: Evaluate maintenance expenses to find savings opportunities without sacrificing quality. Consider refining inventory controls, simplifying work processes, or enhancing preventive care approaches.
Preventive Care: Assess maintenance timing and methods against industry standards. Think about adding condition monitoring to catch problems early, preventing expensive failures.
Task Management: Study work order patterns to spot process delays. Look at streamlining request creation, approval steps, and team communication to boost efficiency.
Performance Metrics: Monitor crucial indicators like repair response times, maintenance schedule compliance, and equipment effectiveness. These measurements help identify where improvements are needed.
Investment Returns: Compare performance data from before and after CMMS implementation. This helps demonstrate system value and supports continued development.
Optimization Methods
Various approaches support system refinement:
- Performance Analysis: Leverage system reports to uncover trends and improvement opportunities.
- Workflow Assessment: Document maintenance procedures to identify inefficient steps.
- Problem Investigation: Examine equipment failure causes to develop better prevention strategies.
Through consistent attention to these areas, organizations can realize increasing benefits from their CMMS investment.
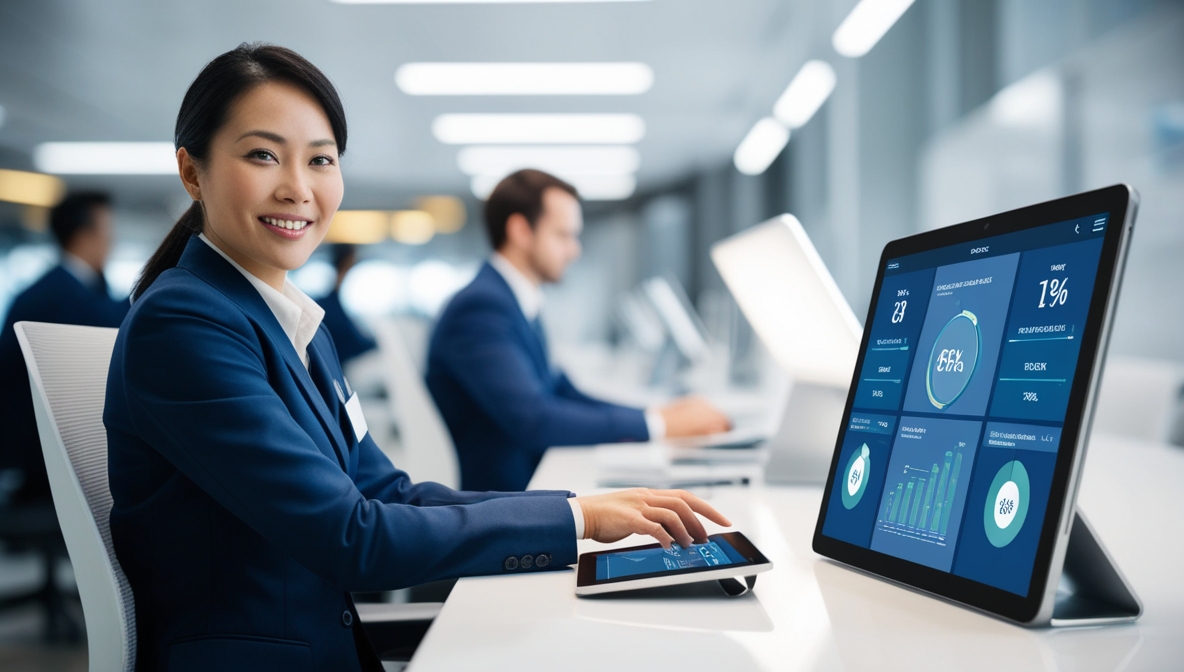
Managing CMMS Implementation Hurdles
While CMMS offers valuable benefits, organizations typically face several hurdles during deployment. Understanding these obstacles helps teams prepare effective solutions and achieve better outcomes.
Common implementation roadblocks include:
- Project Derailment: Poor preparation, insufficient user coaching, low adoption rates, or mismatched system selection can halt progress.
- Performance Issues: Successfully installed systems may still underperform without proper usage guidelines and regular updates.
- Staff Hesitation: Team members might resist new technology due to uncertainty, learning curves, or workload concerns.
- Record Transfer Problems: Moving maintenance data proves complex, with potential accuracy and completeness issues during migration.
Solutions and Strategies
Address these challenges using proven approaches:
- Transition Planning: Create comprehensive change management strategies addressing staff concerns while highlighting system advantages and providing robust training support.
- Clear Updates: Keep all stakeholders informed through regular, transparent communication about timelines, milestones, and plan adjustments.
- Learning Resources: Deliver thorough user training alongside ongoing assistance through help centers, online guides, and internal system experts.
- Data Standards: Maintain information quality through careful verification before, during, and after system transition.
Implementing these strategies early helps organizations navigate common pitfalls and maximize their CMMS investment benefits.
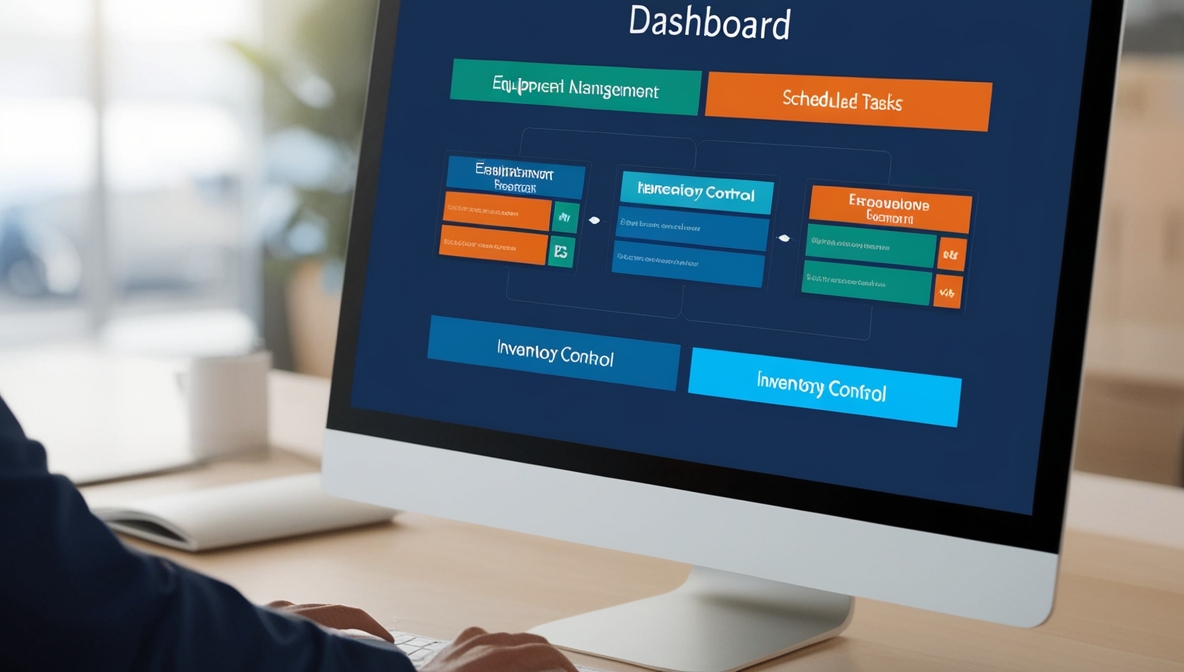
Wrapping Up: CMMS Implementation Success
Embracing Continuous Improvement
CMMS deployment represents an ongoing journey rather than a fixed destination. Success demands thorough planning, methodical execution, and dedication to constant refinement. Following implementation best practices while actively addressing potential hurdles helps organizations achieve optimal results from their maintenance management systems.
A properly implemented CMMS revolutionizes maintenance operations, delivering marked improvements in efficiency, cost control, equipment reliability, and workplace safety. Organizations gain the ability to shift from reactive repairs to data-driven preventive maintenance, enhancing overall operational performance and financial outcomes.
Expert Support for Your CMMS Journey
Makini provides comprehensive CMMS solutions tailored for organizations of all sizes seeking to enhance their maintenance operations. Our experienced team guides clients through every implementation phase - from initial strategy and system selection through data migration, staff training, and ongoing assistance. We understand common implementation challenges and provide the expertise needed for success.
Looking to transform your maintenance program with powerful yet user-friendly CMMS tools? Connect with Makini today to explore our solutions and learn how we can support your successful system implementation.
Frequently Asked Questions (FAQ)
How do industry requirements affect CMMS setup?
Different sectors face unique regulations and operational needs requiring specific CMMS configurations. Food producers must meet strict safety standards, while pharmaceutical companies need robust quality controls. Your CMMS should accommodate these industry-specific demands.
What's the best way to measure CMMS value?
Track key metrics like reduced downtime, lower maintenance costs, better asset usage, and improved productivity. Establish baseline measurements before implementation to demonstrate system benefits.
Which implementation mistakes should we avoid?
Watch out for unclear objectives, low stakeholder involvement, poor data quality, inadequate training, and choosing overly complex or limited systems.
How can we encourage system adoption?
Include users in selection and setup, provide role-specific training, maintain support resources, emphasize benefits, and recognize early adopters.
What about connecting with other business systems?
CMMS integration options vary by vendor - some offer pre-built connections while others provide custom integration tools. Evaluate these capabilities during selection and include integration in your implementation plan.