In the labyrinth of modern business operations, work orders serve as the golden thread that guides maintenance teams through their daily challenges. Like skilled conductors leading an orchestra, facility management professionals orchestrate countless maintenance tasks, each requiring precise timing and execution.
The best work order software has emerged as their essential score sheet, transforming chaotic maintenance requests into a harmonious flow of operational excellence. This transformation has been further accelerated by integration platforms like Makini, which enable seamless connections between maintenance systems and other critical business applications through a unified API.
Picture a manufacturing facility where maintenance activities once resembled a game of telephone - messages garbled, priorities confused, and technicians racing from one emergency to another. This reactive dance of maintenance and repair created a perpetual cycle of downtime and frustration. Today's work order management software has rewritten this familiar script, introducing a new era where every service request flows through a sophisticated system of checks and balances.
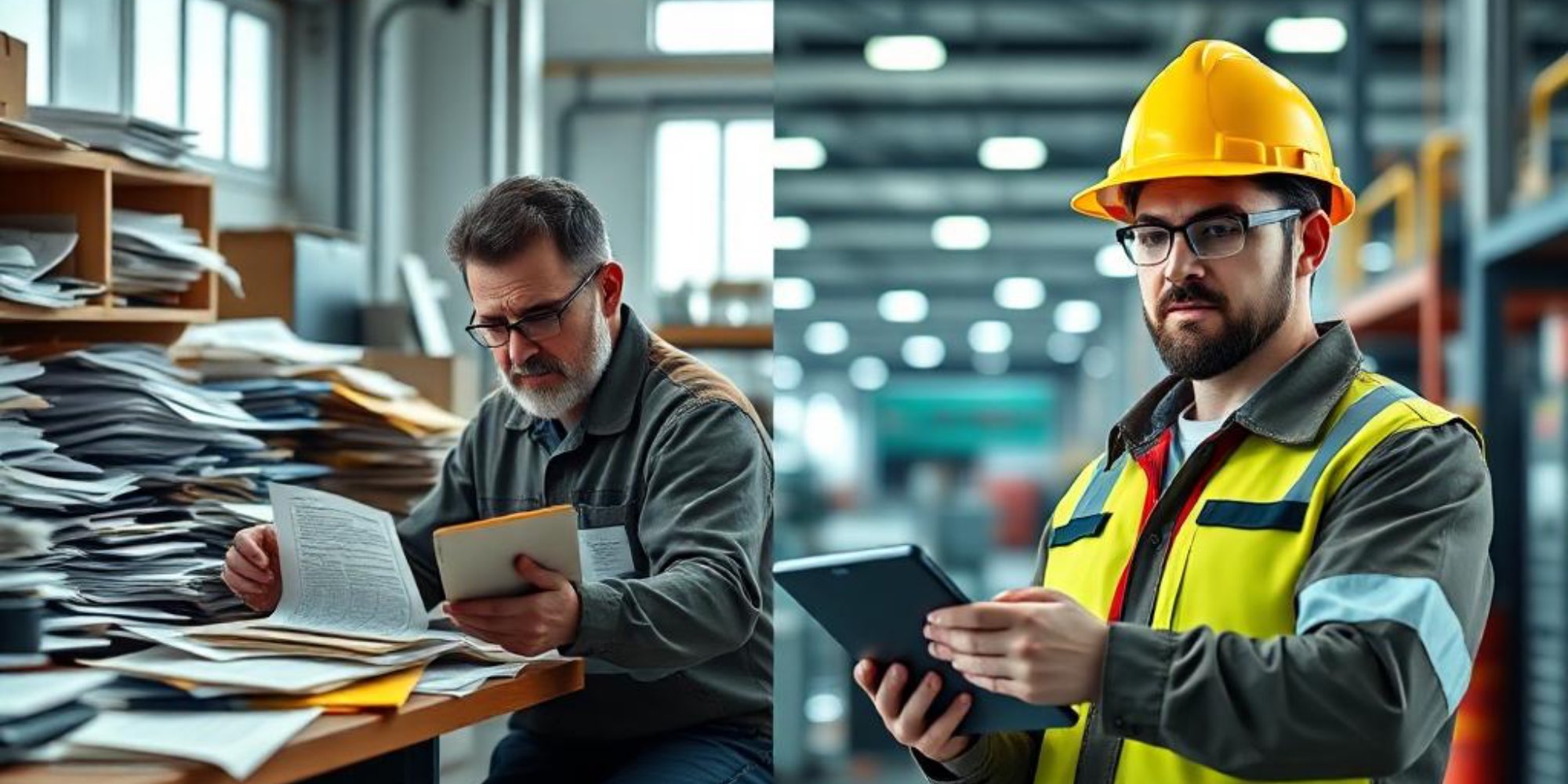
The transformation runs deeper than mere digitization. When a maintenance request enters a modern work order management system, it triggers a cascade of intelligent processes that would have seemed like science fiction just a decade ago. Technicians receive real-time notifications, complete with detailed histories and maintenance schedules. Field service management becomes less about fighting fires and more about preventing them from starting in the first place.
Consider the evolution of preventive maintenance within this ecosystem. Organizations have graduated from simple calendar-based schedules to sophisticated predictive maintenance approaches. The software helps maintenance teams track work with unprecedented precision, ensuring that no preventative maintenance task falls through the cracks. This systematic approach to equipment maintenance has revolutionized how facilities maintain their operational heartbeat.
The true artistry of modern work order software lies in its ability to streamline maintenance operations while adapting to each organization's unique rhythm. Whether managing a single facility or coordinating maintenance across multiple locations, the software allows teams to automate routine tasks while maintaining the flexibility to handle unexpected challenges. Field service technicians, once tethered to paper worksheets and radio dispatches, now carry powerful mobile tools that transform how they complete work orders and document their progress.
The Transformation of Maintenance Through Digital Intelligence
The sophistication of modern work order software extends far beyond basic task tracking, creating an ecosystem where every maintenance activity becomes part of a larger operational symphony. When a new work order enters the system, it doesn't merely represent a task to be completed - it becomes a data point in an organization's ongoing journey toward maintenance excellence.
Consider how preventive maintenance has evolved under this digital transformation. Traditional maintenance schedules once existed as static documents, relegated to dusty binders or forgotten spreadsheets. Today's work order management software transforms these schedules into living systems that adapt and learn. The software provides maintenance teams with dynamic tools to track work progress, analyze equipment performance patterns, and adjust maintenance activities based on real-world conditions.
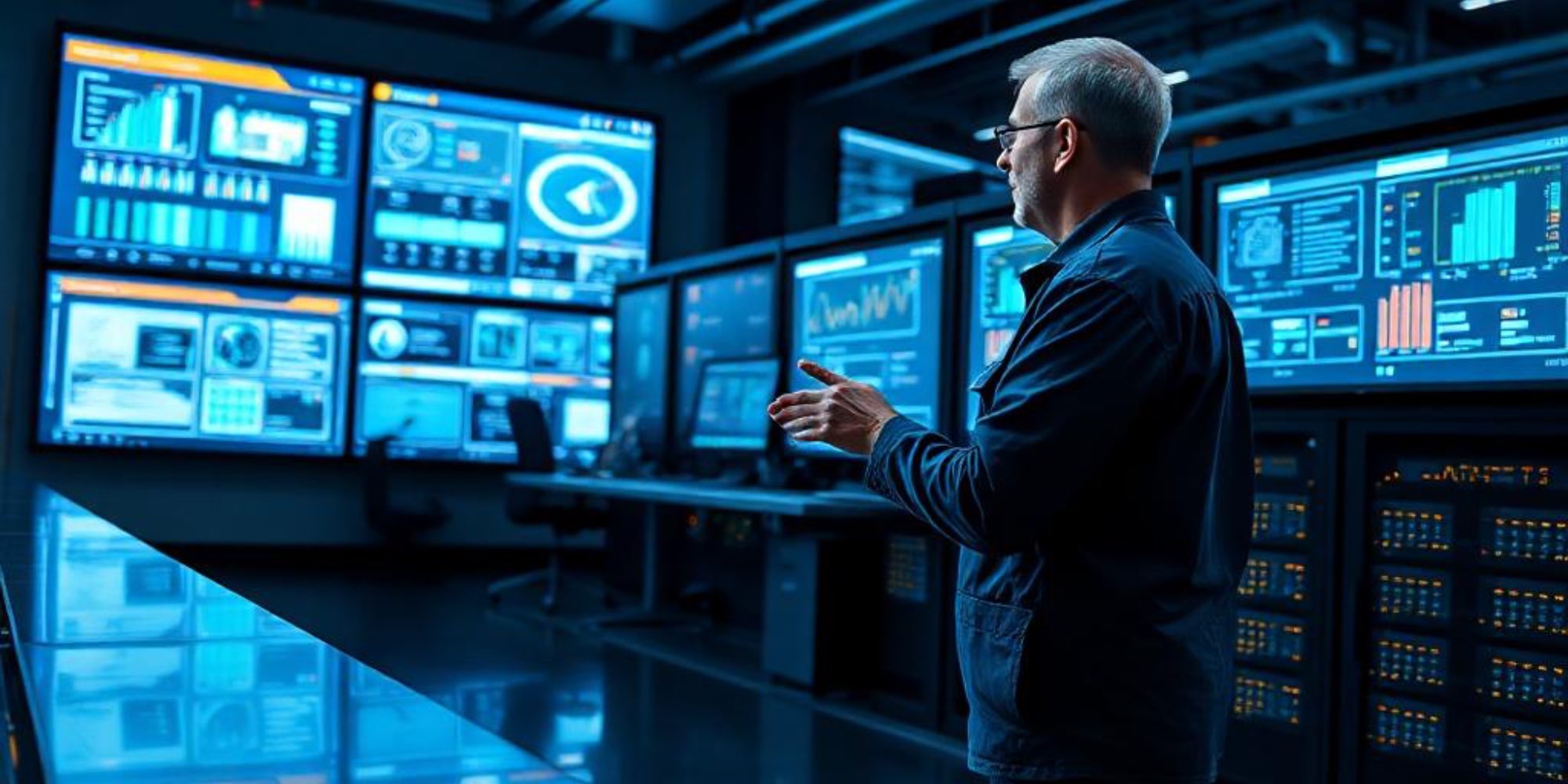
Field service management has undergone an equally profound metamorphosis. Where technicians once navigated their daily rounds with limited information and reactive priorities, they now operate within an intelligent network that helps streamline their every move. The mobile-first approach of modern work order solutions ensures that field service professionals can access complete maintenance histories, detailed repair procedures, and real-time updates from any location.
The impact on operational efficiency becomes particularly evident in how organizations manage their assets. Asset management software integrated with work order systems creates a comprehensive view of equipment health and maintenance needs. When maintenance teams assign work order tasks, they do so with complete visibility into each asset's history, performance metrics, and maintenance requirements. This depth of information transforms how technicians approach their work, enabling them to complete work orders with greater precision and effectiveness.
The software allows organizations to move beyond simple task management into the realm of predictive operations. By tracking maintenance patterns and equipment performance over time, maintenance teams can identify potential issues before they develop into costly problems. This proactive approach to maintenance and repair has revolutionized how facilities manage their resources and minimize downtime.
From Theory to Practice: Mastering Work Order Implementation
Understanding how to effectively implement work order software requires more than technical knowledge - it demands a fundamental shift in how organizations approach maintenance management. Think of it as learning a new language where every maintenance request becomes part of a broader conversation about operational excellence.
The journey begins with understanding how work orders flow through an organization's ecosystem. Much like water finding its natural course, maintenance activities need clear channels and well-defined paths. When organizations implement a work order management system, they're not simply installing software - they're creating a new operational framework where every maintenance task, from simple repairs to complex preventive maintenance schedules, follows an optimized path to completion.
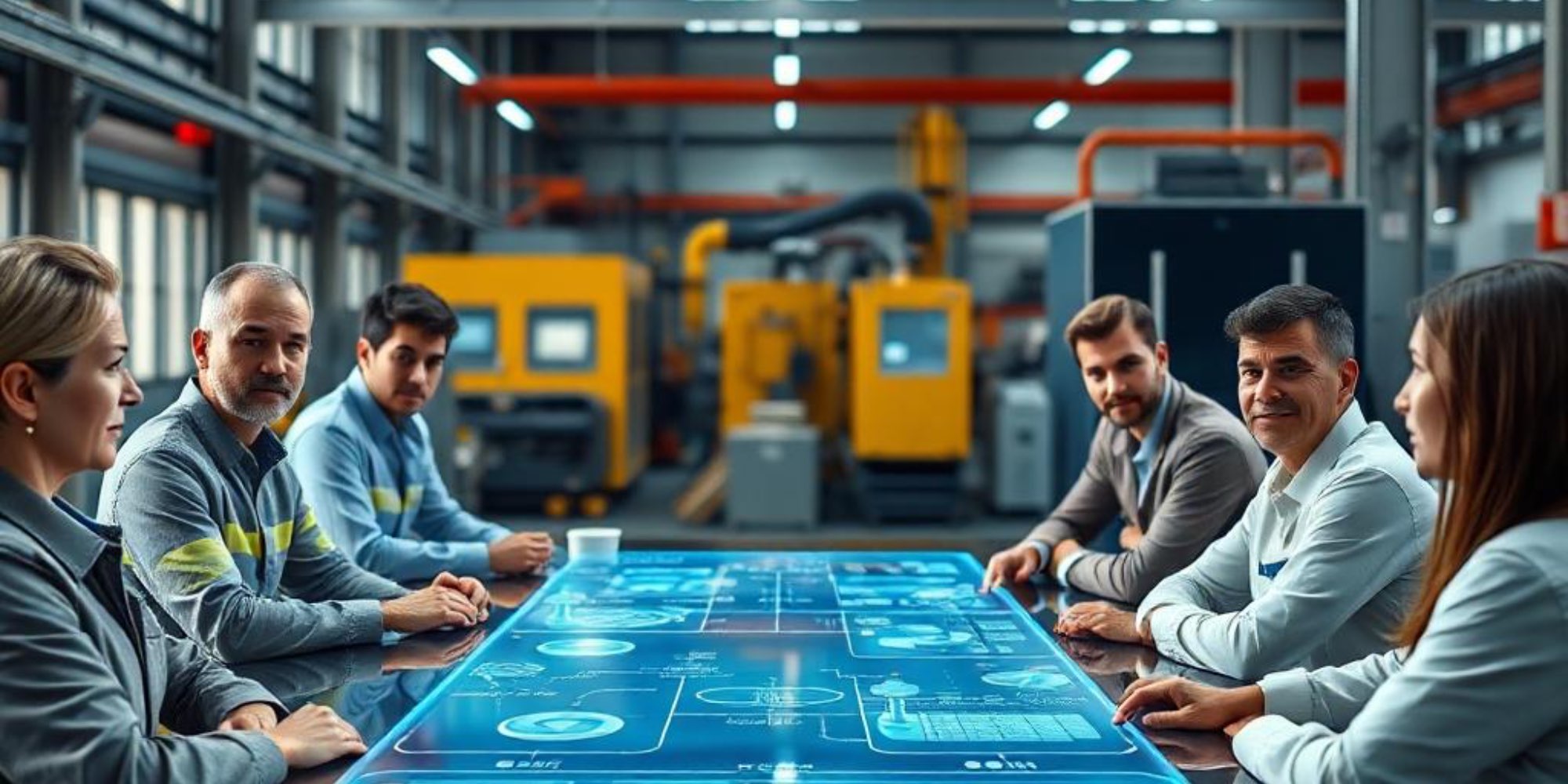
Consider how this transformation affects the daily lives of maintenance teams. A technician arriving for their morning shift no longer faces a chaotic pile of paper requests or a flood of urgent calls. Instead, the work order software provides a structured approach to their day. Each new work order appears with crucial context - equipment histories, maintenance procedures, and real-time priority updates. This systematic organization helps streamline maintenance processes while ensuring that no critical tasks slip through the cracks.
The implementation of preventive maintenance capabilities represents perhaps the most significant shift in operational thinking. Traditional reactive approaches, where teams rushed from one emergency to another, give way to sophisticated scheduling systems that help prevent problems before they occur. The software allows maintenance teams to establish comprehensive maintenance schedules that account for equipment lifecycles, usage patterns, and historical performance data. This transition to preventative maintenance marks a fundamental evolution in how organizations approach asset management and operational efficiency.
Field service management undergoes a similar transformation. Mobile-first work order solutions enable technicians to operate with unprecedented efficiency in the field. When they receive a service request, they have immediate access to all relevant information - from detailed maintenance histories to specific repair procedures. This real-time availability of critical data helps transform how field service teams complete work orders and document their progress.
The Symphony of Advanced Work Order Management
Just as a master musician moves beyond basic scales to create complex compositions, organizations must learn to leverage advanced work order software features to orchestrate truly efficient maintenance operations. The sophistication of modern solutions transforms the fundamental nature of how maintenance teams operate, creating new possibilities for operational excellence.
Consider the evolution of preventive maintenance in this advanced ecosystem. Modern work order software doesn't simply schedule routine tasks - it creates an intelligent framework for predicting and preventing equipment failures. When maintenance teams establish preventive maintenance tasks, they tap into sophisticated algorithms that analyze equipment performance patterns, usage data, and historical maintenance records. This deep integration helps organizations move beyond basic preventative maintenance into the realm of predictive maintenance, where potential issues are identified and addressed before they impact operations.
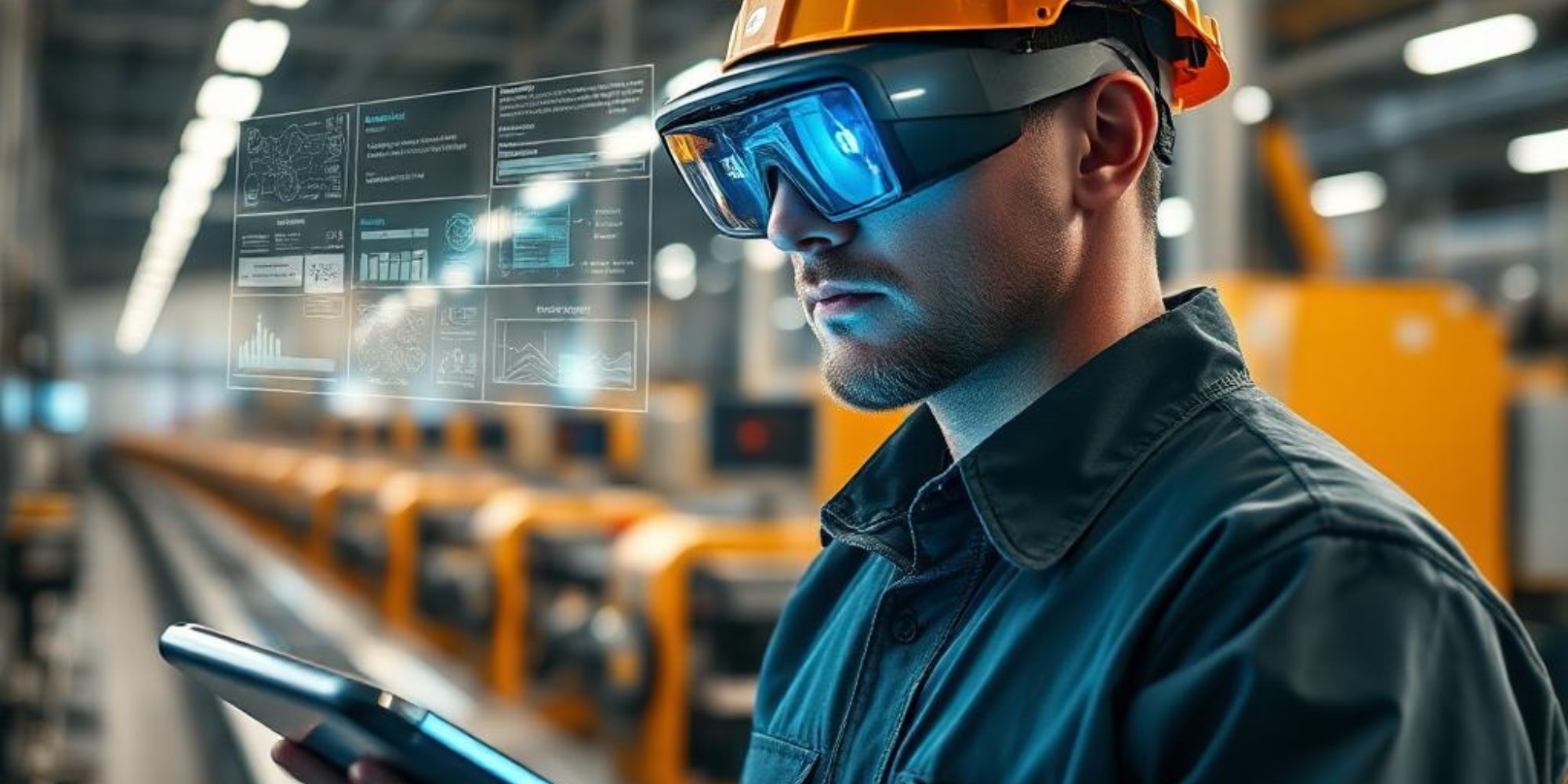
The transformation of field service management illustrates another dimension of this technological evolution. Today's technicians operate within a dynamic information ecosystem that helps streamline every aspect of their work. When a new work order appears in their mobile interface, it arrives complete with contextual data that transforms their ability to complete work efficiently. Think of it as having a master mechanic's knowledge base instantly available at every job site.
Real-time communication capabilities have revolutionized how maintenance teams coordinate their efforts. The software allows instant updates and collaboration between field technicians, supervisors, and facility management professionals. When a technician encounters an unexpected challenge during a maintenance request, they can immediately access expert guidance or request additional resources. This seamless communication flow helps reduce downtime and ensures that maintenance activities proceed with minimal disruption.
Asset management integration represents perhaps the most powerful advancement in modern work order systems. Organizations can now track every aspect of their equipment lifecycle within a single unified platform. When maintenance teams manage work orders, they do so with complete visibility into asset histories, performance metrics, and maintenance requirements. This comprehensive approach to asset management transforms how organizations plan and execute their maintenance strategies, enabling more informed decisions about resource allocation and equipment replacement cycles.
The Future of Maintenance Excellence: Emerging Trends and Technologies
As we look toward the horizon of maintenance management, the evolution of work order software continues to reshape how organizations approach their operational challenges. Much like the transition from analog to digital transformed the music industry, emerging technologies are fundamentally changing how maintenance teams track work, manage assets, and optimize their daily operations.
Artificial Intelligence and Machine Learning are revolutionizing how organizations handle maintenance requests. Modern work order management systems now incorporate predictive algorithms that analyze patterns across thousands of service requests, equipment performance metrics, and maintenance records. This sophisticated analysis helps maintenance teams move beyond basic preventive maintenance into truly predictive maintenance strategies. Imagine a system that not only alerts you to potential equipment failures but also suggests the optimal timing for maintenance interventions based on real-world operational patterns.
The mobile revolution in field service management continues to accelerate. Today's technicians carry powerful diagnostic tools in their pockets, with work order software that provides unprecedented access to maintenance schedules, equipment histories, and repair procedures. When a new work order enters the system, artificial intelligence helps assign it to the most qualified technician based on expertise, location, and current workload. This intelligent distribution of maintenance tasks helps streamline operations while ensuring optimal resource utilization.
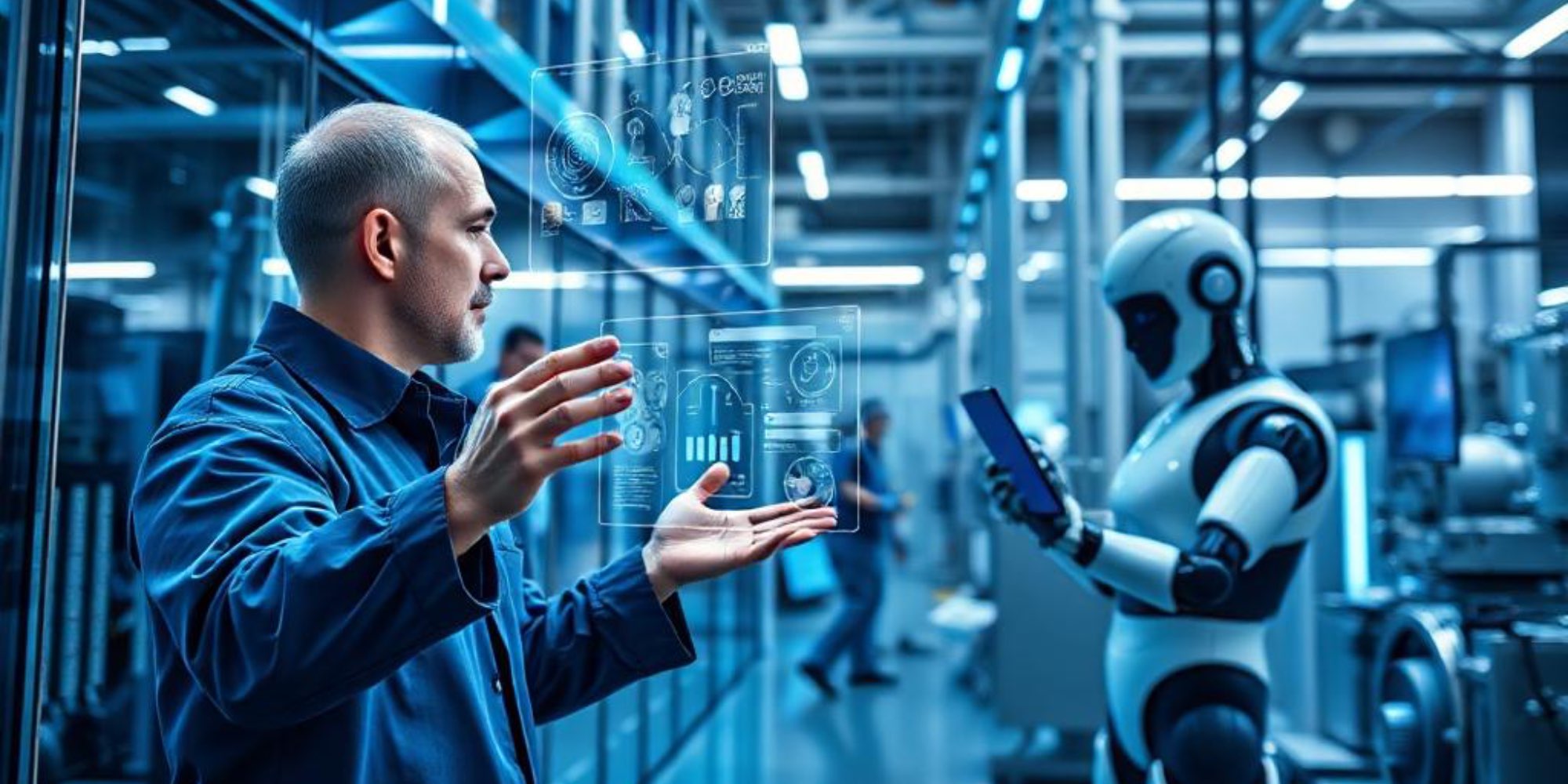
The integration of Internet of Things (IoT) sensors with work order systems represents another quantum leap in maintenance management. Equipment now communicates directly with maintenance management software, automatically generating service requests when performance metrics indicate potential issues. This direct communication helps organizations track maintenance needs with unprecedented precision, reducing downtime through early intervention and more effective preventative maintenance scheduling.
Looking ahead, the convergence of augmented reality with work order management promises to transform how technicians complete work in the field. Imagine a maintenance professional approaching a piece of equipment and seeing not just its current status but its entire maintenance history, step-by-step repair procedures, and real-time diagnostic data overlaid directly in their field of view. This technology will help streamline maintenance operations while reducing errors and improving first-time fix rates.
The future of asset management lies in creating digital twins - virtual replicas of physical equipment that enable maintenance teams to simulate different maintenance scenarios and optimize their strategies before implementing them in the real world. When integrated with work order software, these digital twins will provide unprecedented insight into how maintenance decisions impact equipment performance and longevity.
As we stand at this technological crossroads, one truth becomes clear: the organizations that thrive will be those that embrace these innovations while maintaining focus on their fundamental maintenance objectives. The best work order software of tomorrow will not just manage maintenance tasks - it will serve as an intelligent partner in achieving operational excellence.
In this evolving landscape, the role of maintenance professionals transforms from reactive problem-solvers to proactive strategists. By leveraging sophisticated work order management systems, organizations can create maintenance operations that are more efficient, more predictable, and more aligned with their strategic objectives. The future of maintenance management has arrived, and it promises to be more intelligent, more connected, and more capable than ever before.
A Deep Dive into Industry-Leading Work Order Solutions
Just as a craftsman must choose the right tools for their trade, organizations must carefully select the best work order software that aligns with their maintenance management needs. Let's examine the leading solutions that have emerged as true masters of maintenance orchestration in 2024.
UpKeep
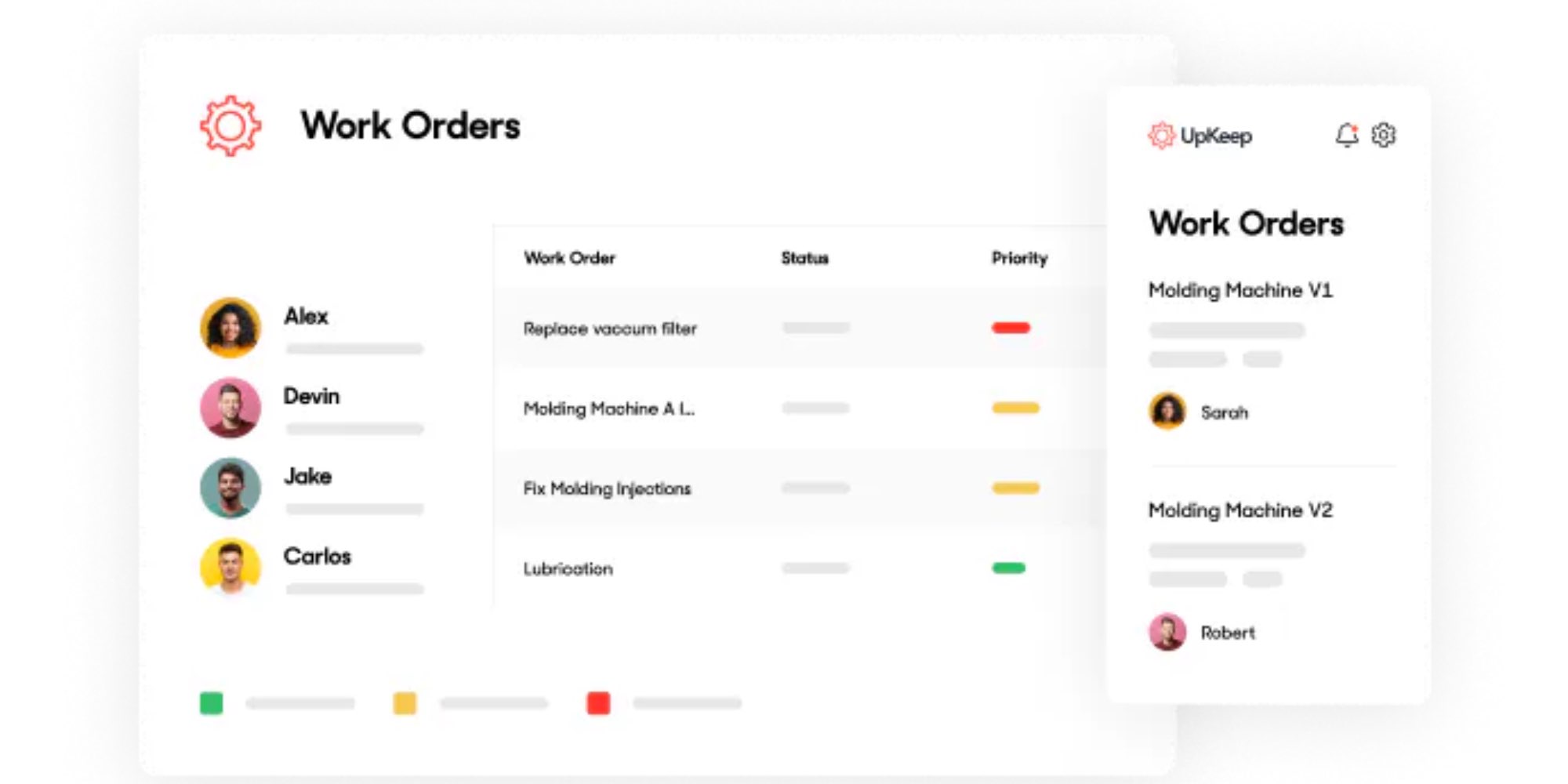
In the realm of work order management, UpKeep has established itself as a revolutionary force, particularly in how it approaches field service management. What sets this solution apart is its extraordinary mobile-first philosophy - imagine having the power of an entire maintenance command center in your pocket. When technicians receive a new work order, they gain instant access to a wealth of information: equipment histories, maintenance schedules, and repair procedures, all thoughtfully organized at their fingertips.
The software provides exceptional tools for preventive maintenance scheduling, allowing organizations to transition smoothly from reactive firefighting to proactive maintenance strategies. The platform's real-time tracking capabilities ensure that maintenance teams can monitor work orders with unprecedented precision, while its intuitive interface helps streamline maintenance operations across multiple facilities.
MaintainX
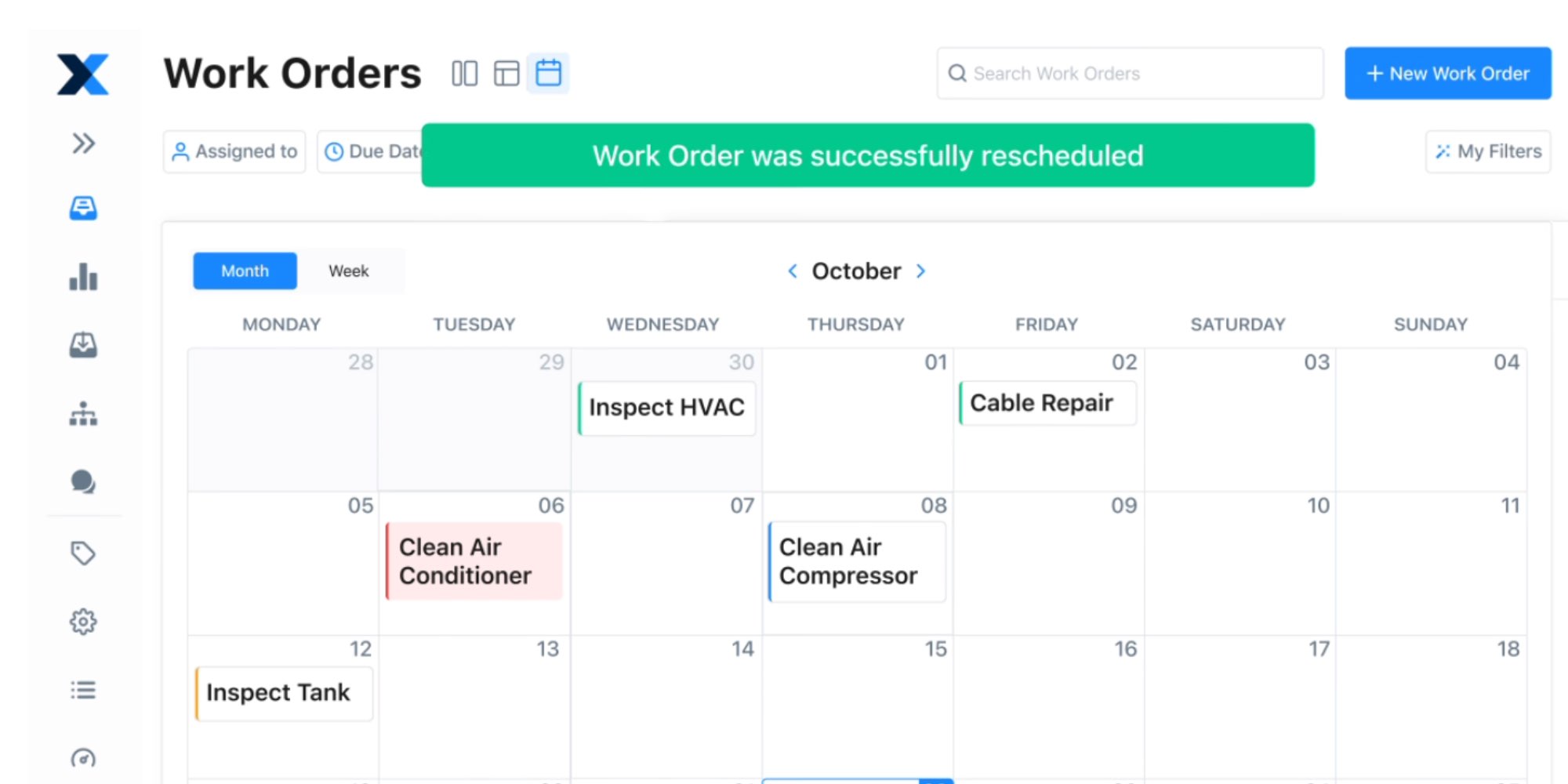
MaintainX approaches work order management with a unique focus on team collaboration and communication clarity. Think of it as a digital roundtable where maintenance teams, facility management professionals, and field service technicians gather to orchestrate their maintenance activities with perfect harmony. The software helps organizations track work progress while maintaining clear lines of communication between all stakeholders.
Hippo CMMS
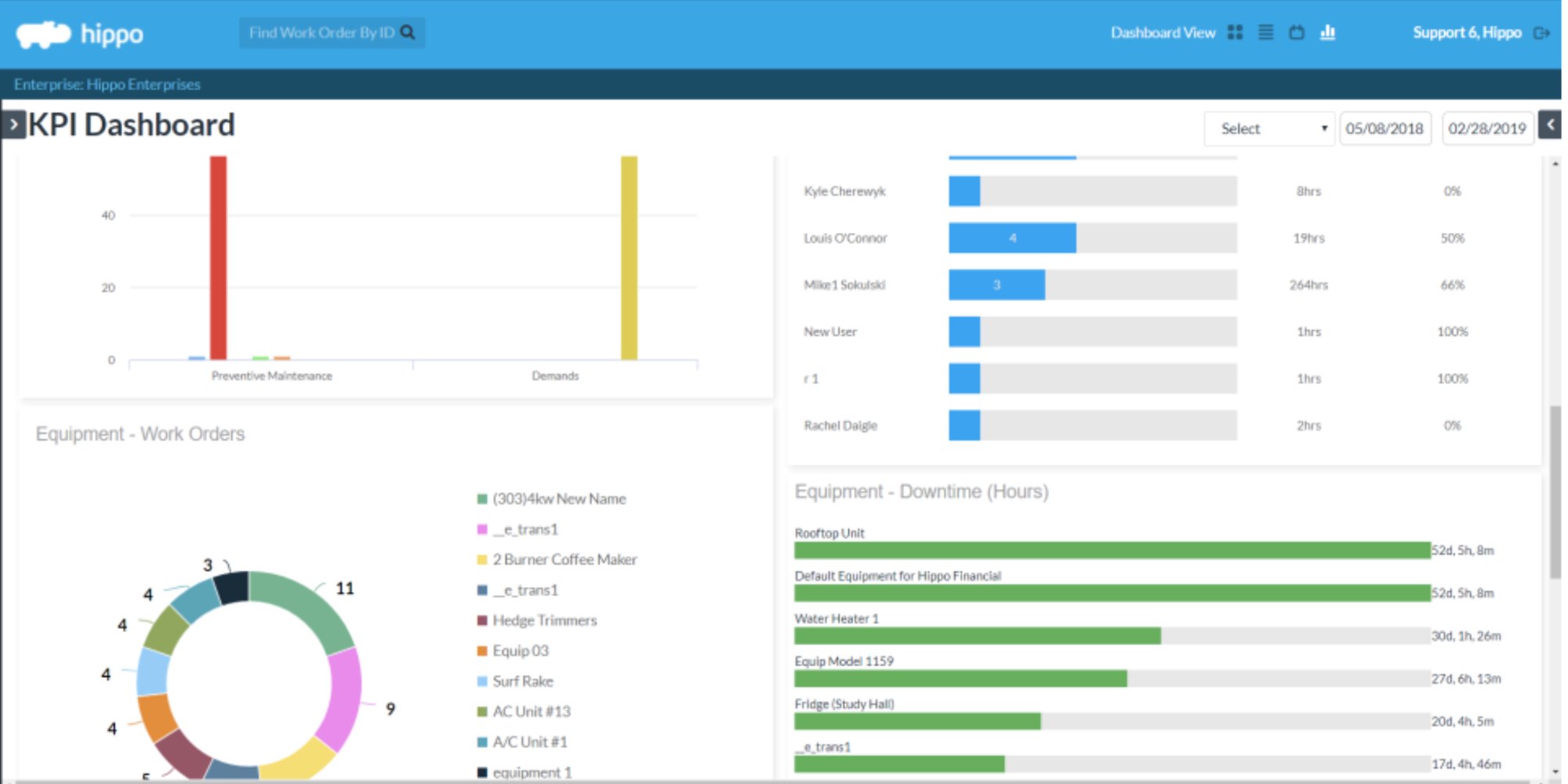
In the complex symphony of enterprise maintenance, Hippo CMMS stands as a masterful conductor, orchestrating sophisticated work order management for large-scale operations. This comprehensive computerized maintenance management system excels in environments where multiple facilities require coordinated maintenance activities. When maintenance teams need to track work across diverse locations, Hippo CMMS provides the sophisticated oversight and control necessary for seamless operations.
What truly distinguishes Hippo CMMS is its robust approach to preventive maintenance scheduling. The software helps organizations create intricate maintenance schedules that account for every piece of equipment, much like a conductor ensuring each instrument enters at precisely the right moment. This systematic approach to maintenance tasks significantly reduces equipment downtime while extending asset lifecycles through careful monitoring and timely interventions.
Fiix
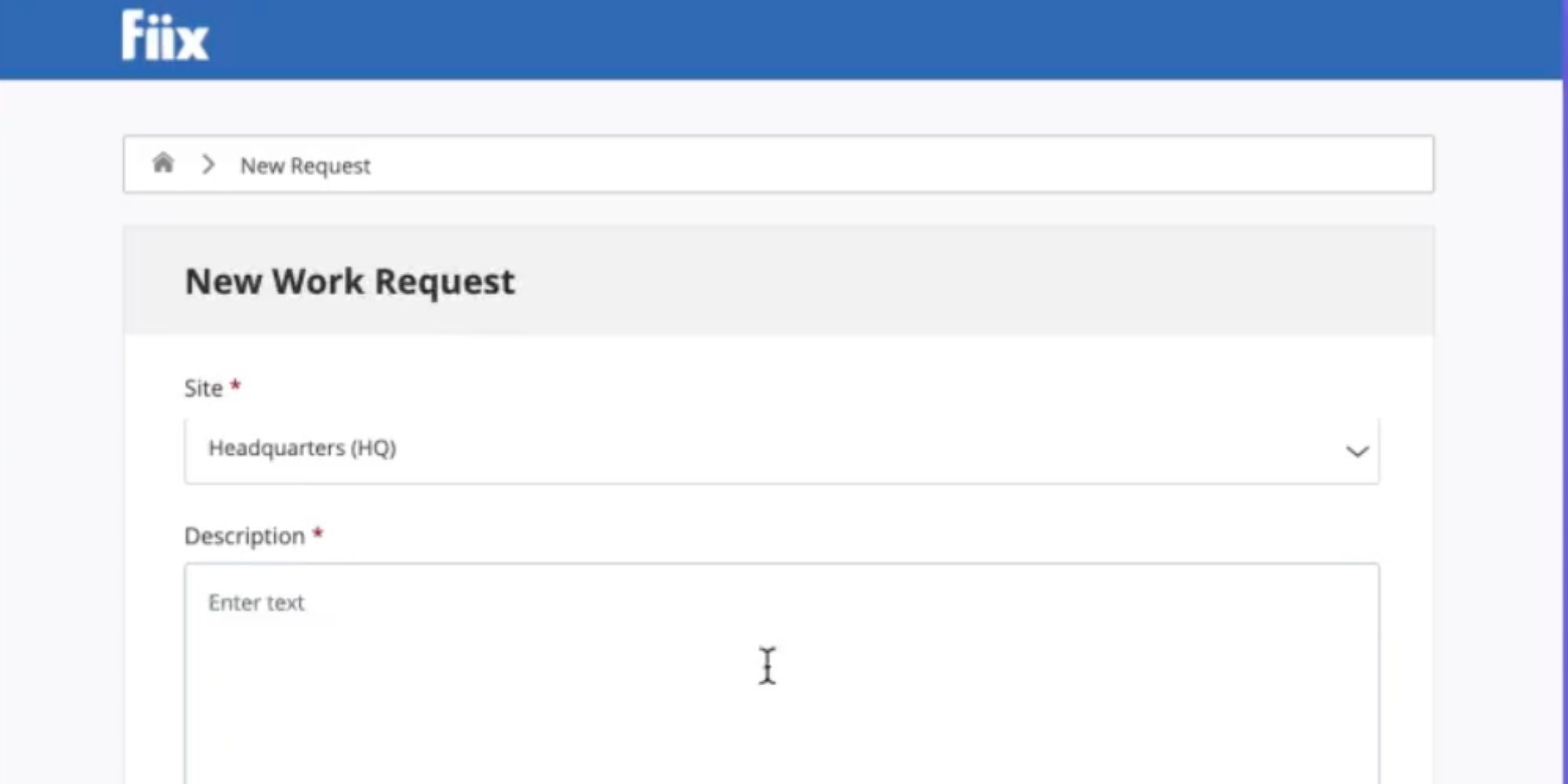
Fiix has revolutionized how organizations approach maintenance management through its sophisticated cloud-based architecture. Think of it as having a maintenance command center accessible from anywhere in the world. When technicians assign work order tasks, they tap into a unified platform that seamlessly connects field service management with comprehensive asset management capabilities.
The software's strength lies in its ability to help organizations transition from reactive to predictive maintenance strategies. Through advanced analytics and real-time tracking capabilities, maintenance teams can identify patterns in equipment performance and maintenance needs before issues arise. This proactive approach to maintenance and repair has transformed how facilities manage their resources and optimize their operational efficiency.
eMaint CMMS
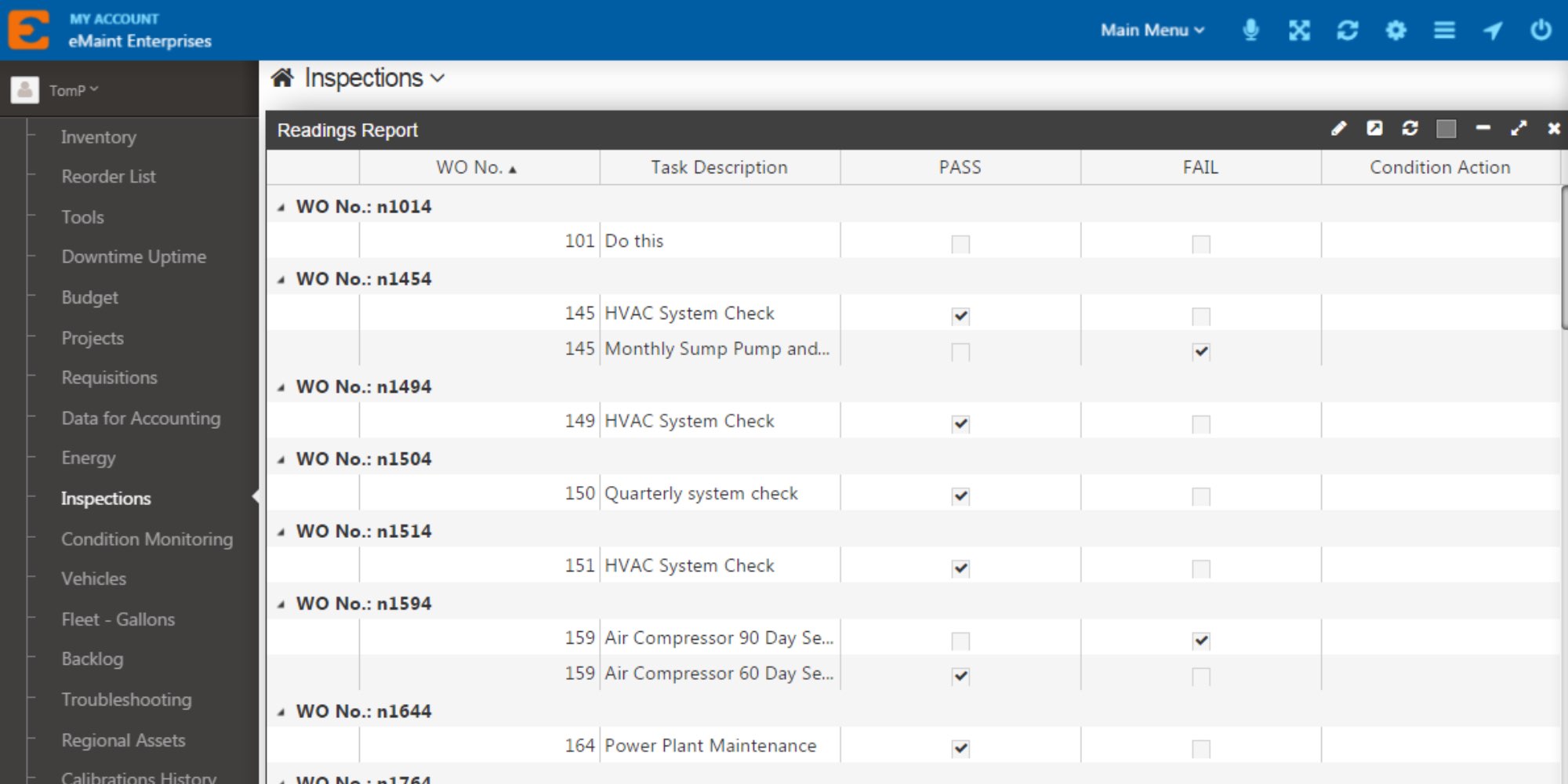
eMaint CMMS has carved its niche by offering unparalleled customization capabilities in the work order software landscape. Like a master tailor crafting a perfect fit, eMaint allows organizations to shape their maintenance management system to match their exact specifications. The platform particularly shines in regulated industries where precise documentation and compliance tracking are as crucial as the maintenance work itself.
What sets eMaint apart is its sophisticated approach to work order tracking and documentation. When maintenance requests enter the system, they flow through carefully designed workflows that ensure every maintenance task meets both operational requirements and regulatory standards. The software provides exceptional tools for preventative maintenance planning while maintaining detailed records of all maintenance activities.
Integration and Advanced Features Across Platforms
Each of these leading work order solutions offers distinct approaches to common challenges in maintenance management. Consider how they handle core functionalities:
Mobile Accessibility: While UpKeep leads with its mobile-first design, each platform offers robust mobile capabilities that help technicians complete work orders efficiently in the field. The ability to track maintenance status and update work orders in real-time has become essential for modern field service management.
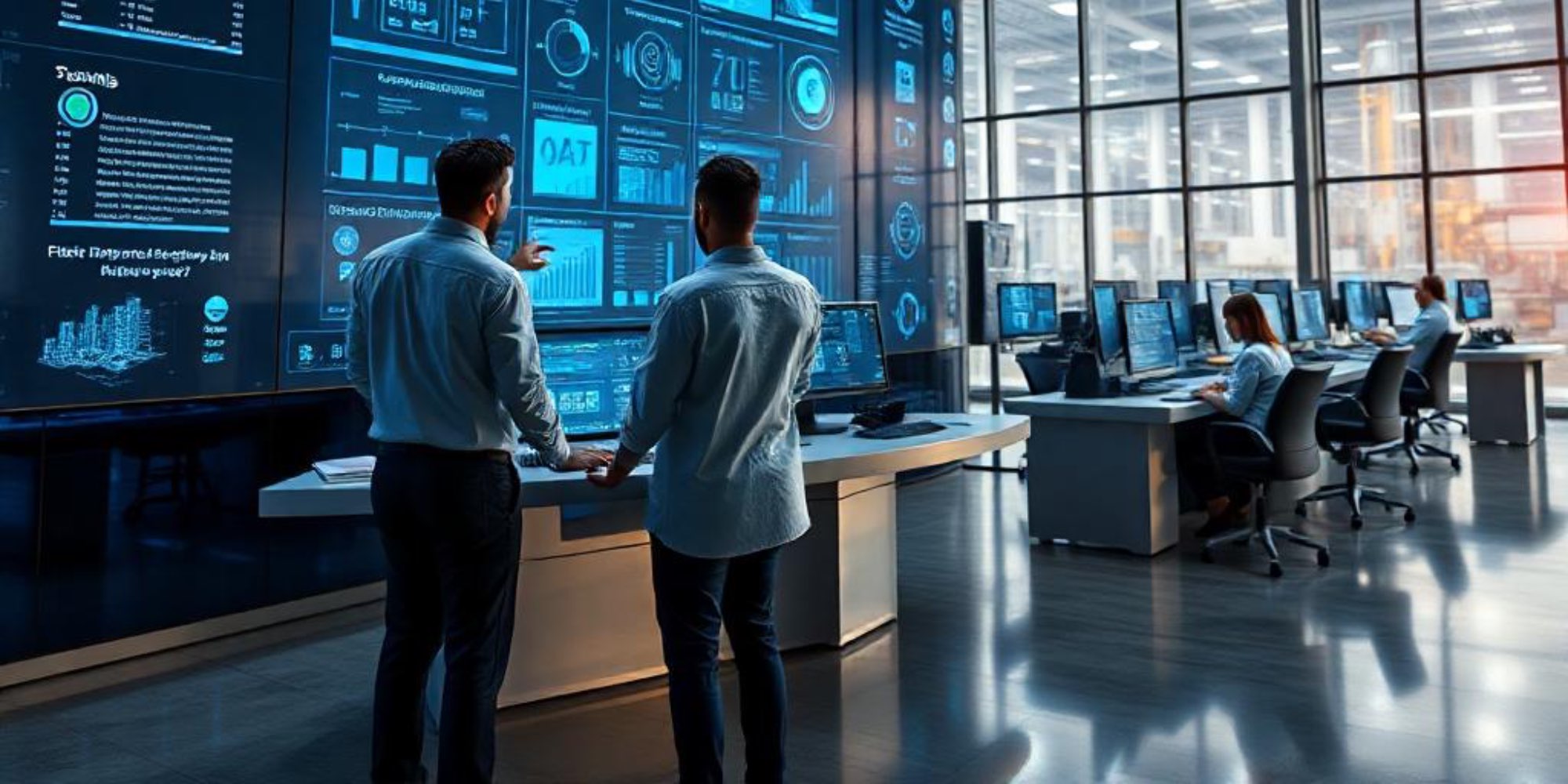
Preventive Maintenance Capabilities: From eMaint's detailed scheduling tools to Hippo CMMS's enterprise-grade maintenance planning, each solution offers sophisticated features to streamline maintenance processes and prevent equipment failures before they occur.
Asset Management Integration: These platforms seamlessly connect work order management with comprehensive asset management features, creating unified systems that help organizations optimize their maintenance operations while extending equipment lifecycles.
The Decision Matrix: Choosing Your Maintenance Partner
Selecting the best work order software requires careful consideration of your organization's specific needs. Consider UpKeep for mobile-intensive operations, MaintainX for communication-heavy environments, Hippo CMMS for enterprise-scale requirements, Fiix for cloud-first operations, and eMaint for highly regulated industries requiring extensive customization.