Introduction
Efficient inventory management is a crucial factor in enhancing productivity in the manufacturing industry. It involves finding the right balance between overstocking and understocking to avoid unnecessary costs and production delays. Organizations like Curriculum Associates have successfully implemented automated distribution systems and warehouse management systems to optimize their inventory management processes. By consolidating facilities and integrating tools like Fishbowl, they have increased capacity and improved inventory tracking, leading to significant cost savings and streamlined operations.
In addition to tools like Fishbowl, advanced systems like Makini also play a vital role in optimizing inventory management. Makini offers solutions such as inventory optimization and integration with Oracle Fusion Cloud warehouse management. These systems enable organizations to maintain optimal inventory levels, prevent overstocking or understocking, and improve overall operational performance. By implementing efficient inventory management practices, businesses can enhance productivity, reduce costs, and ensure smooth production processes.
1. Refining the Material Ordering Process
The quest for enhanced productivity in the manufacturing arena is often kick-started by refining the material ordering process. A well-structured and streamlined system for the procurement of materials can significantly cut down lead times and reduce inventory expenses. Businesses can leverage integrated systems, such as Makini, to bolster their ordering procedures, ensuring materials are requisitioned in the right quantities and at the ideal time.
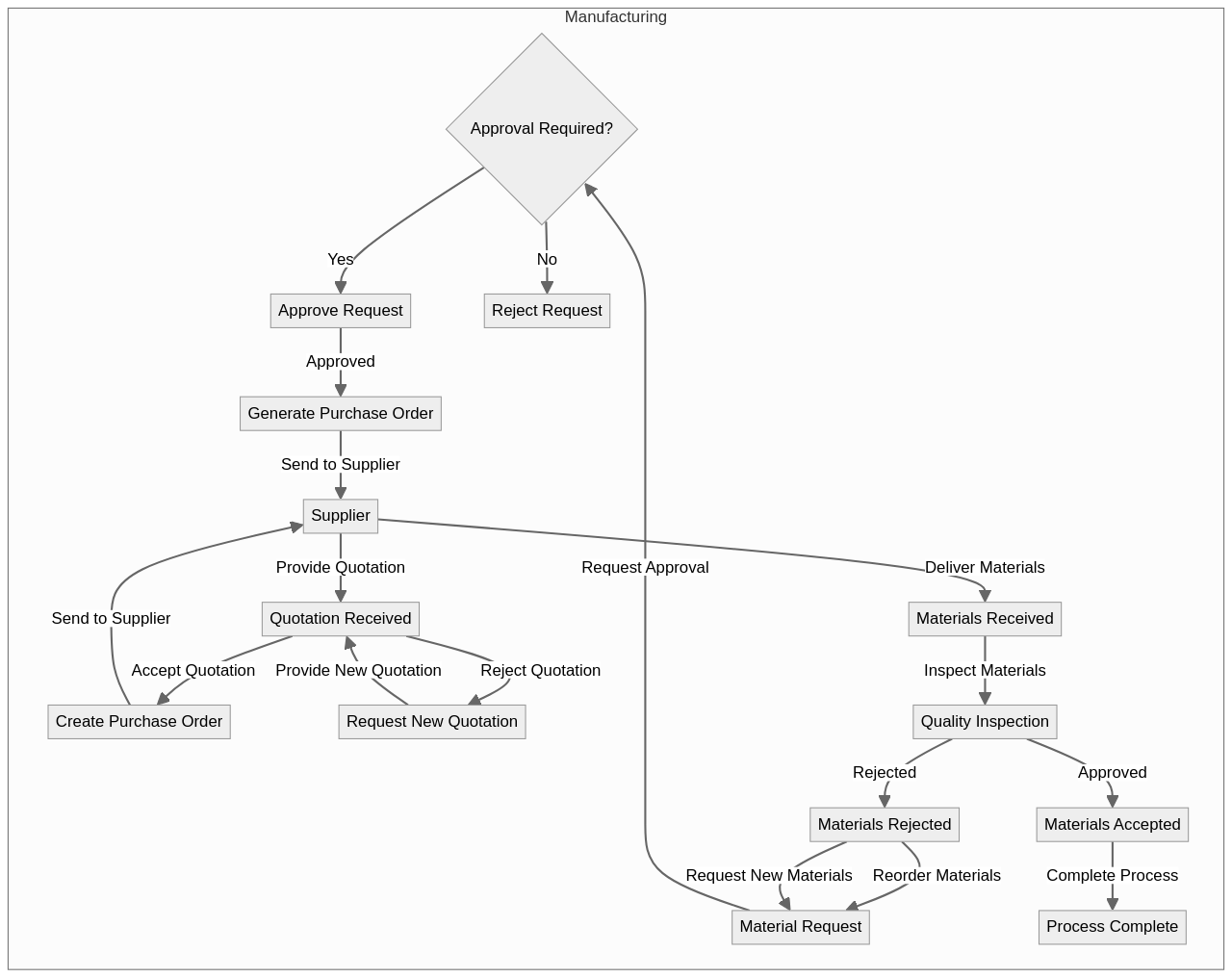
This approach aids in averting overstocking and understocking situations, paving the way for uninterrupted production, and thereby boosting productivity levels.
This process mirrors the refinement of product backlogs in Scrum, a frequently overlooked but essential activity. This involves the breakdown and further definition of backlog items into smaller, more precise items. It's a team effort that requires the entire Scrum team's participation, including developers, relevant stakeholders, and subject matter experts.
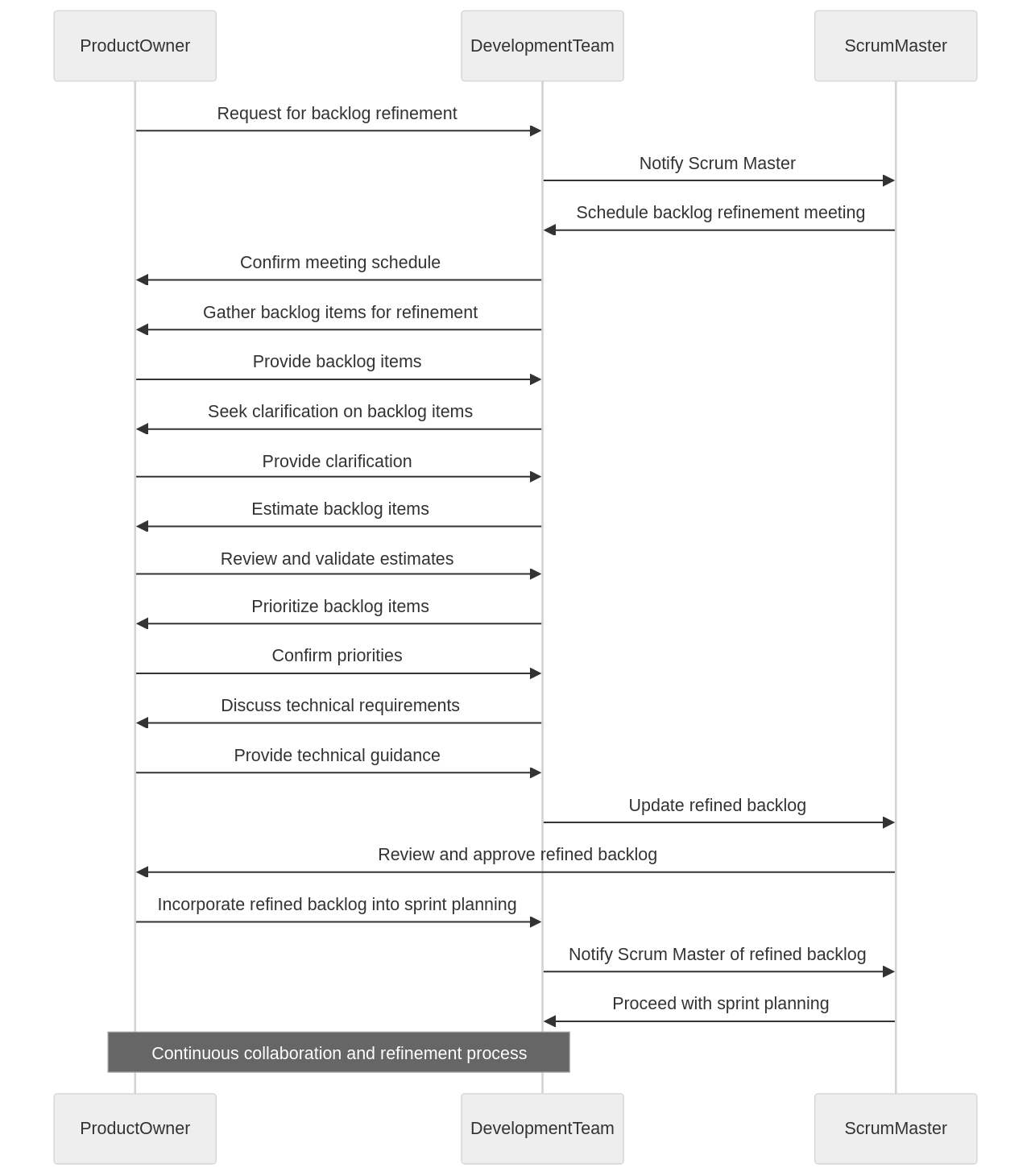
The product owner ensures the backlog is correctly ordered, while developers ensure a clear understanding and proper sizing of backlog items.
Like the material ordering process, items in the backlog are elaborated upon as they ascend the backlog, with more details added as more information is discovered. User stories should be appropriately sized, with a general guideline that no user story should exceed half the duration of the sprint. A 'definition of ready' provides a common understanding of the refinement a user story needs before it is taken on in a sprint. Any updates to the product backlog should be discussed to ensure everyone is on the same page.
The analogy extends to warehouse operations as well, with slotting being a key activity. This involves determining the most suitable storage location for each item in a warehouse. Proper slotting can markedly augment the efficiency of warehouse operations. A basic slotting project entails ranking items based on their frequency of picking and identifying the best locations for them. Factors such as distance, accessibility, and location characteristics are considered when determining the best locations. Other considerations include item size and weight, hazardous items, cold storage items, load building, related items, and zone balancing.
To refine the material ordering process in manufacturing, it's essential to implement certain best practices, such as demand forecasting, vendor management, inventory optimization, standardization, automation, and continuous improvement.
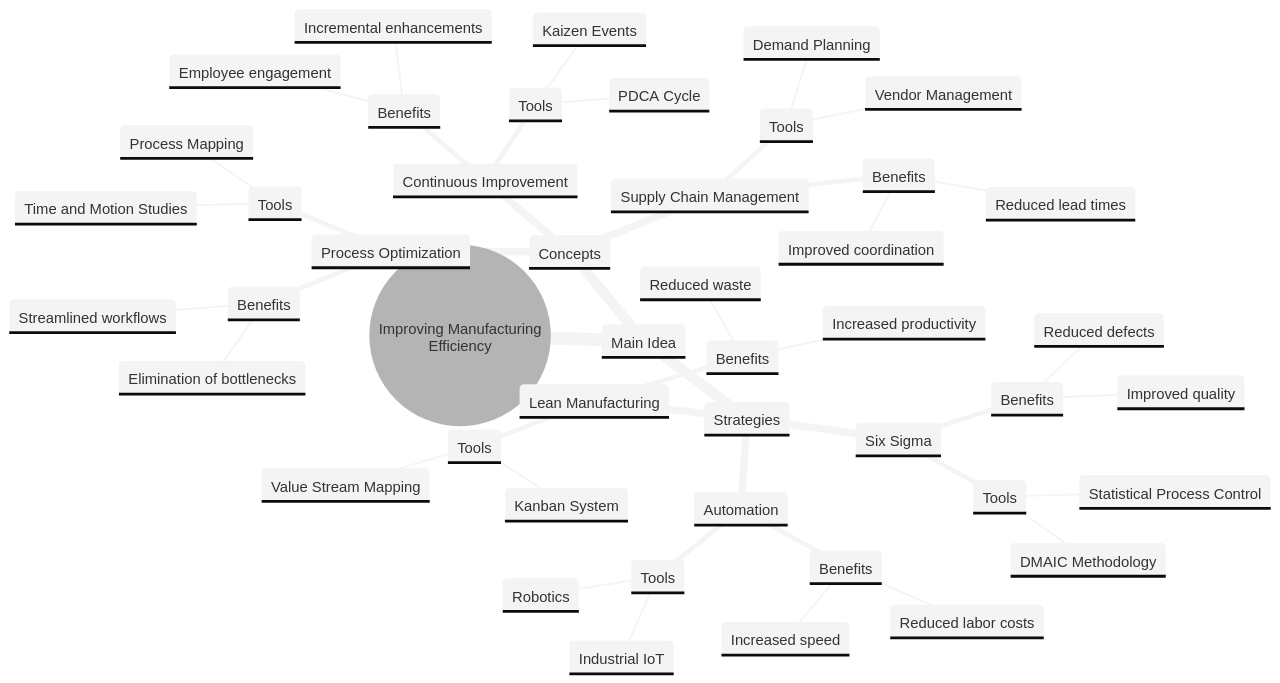
These practices can optimize inventory levels, reduce costs, and ensure timely availability of materials. Makini can be integrated with Oracle Fusion Cloud Warehouse Management or SAP Extended Warehouse Management to automate material ordering processes, improve accuracy, and provide real-time visibility into inventory levels.
Moreover, the reduction of lead times and minimization of inventory costs in material ordering can be achieved by implementing effective strategies, such as streamlining the supply chain, improving demand forecasting, implementing just-in-time inventory management, building strong relationships with suppliers, utilizing technology and automation, and regularly monitoring and evaluating the effectiveness of these strategies.
In summary, refining the material ordering process is akin to the continuous refinement of product backlogs in Scrum and the slotting process in warehouse operations. Each of these processes, when executed effectively, can substantially enhance productivity and operational efficiency.
2. Boosting Manufacturing Productivity by Eliminating Waste
Enhancing productivity within manufacturing essentially revolves around the principle of waste elimination. This idea necessitates the identification and eradication of activities within the production process that do not add value. By examining real-world instances such as Audi's pioneering approach to sustainable manufacturing, we can envision substantial enhancements in productivity and cost savings.
Take Audi, for instance, a leading global player in the automotive industry. They embarked on a sustainability mission that transcended beyond electric vehicles, involving their design and production departments. The challenge they faced was to establish minimal or closed-loop usage of plastics without undermining the quality of automotive components. They discovered a solution in 3devo's SHR3D IT plastic shredder, Airid polymer dryer, and Precision 450 filament maker, enabling Audi to transform their plastic waste into 3D printed tools. This strategy effectively reduced their carbon footprint and production costs.
This practical case study exemplifies the principle of waste elimination. By repurposing plastic waste, Audi succeeded in turning a traditionally non-value-adding activity (disposal of plastic waste) into a value-adding process (creation of 3D printed tools).
Transform your waste into value by integrating Makini with your manufacturing processes.
In the broader perspective of manufacturing, lean methodology offers a guide to waste elimination. This framework categorizes steps within a business or work process that do not generate customer-defined value as wasteful. These non-value-adding activities often encompass time inefficiencies, inaccurate planning, and obsolete practices that yield no customer benefits.
Lean manufacturing categorizes waste into eight types: defects, overproduction, waiting, non-utilized skills and creativity, transportation, excess inventory, motion, and excessive processing. Identifying and eliminating these forms of waste can contribute to significant productivity improvements and cost savings.
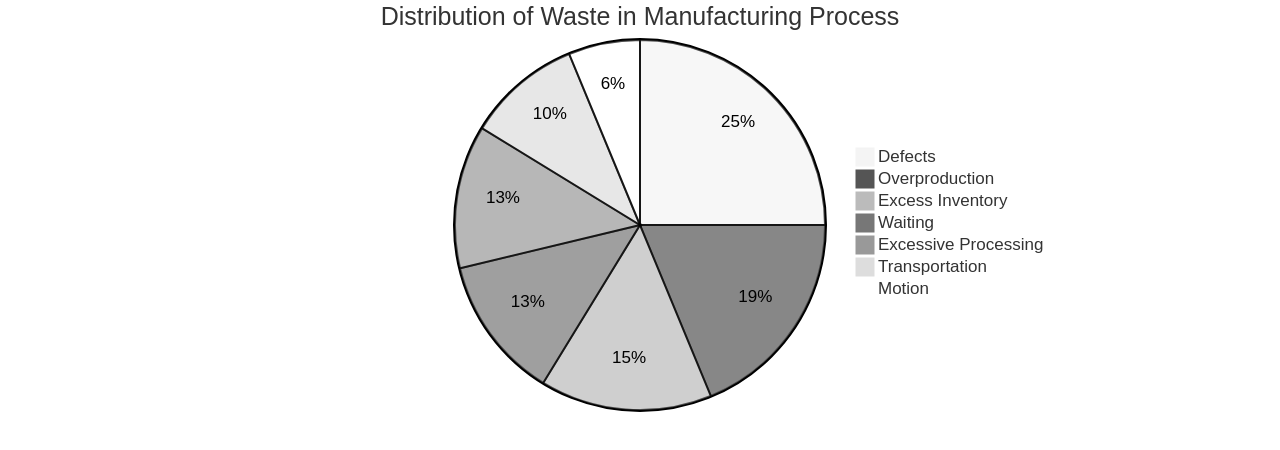
For instance, defects in product quality can result in value stream waste, including scrapped products and additional costs. Overproduction can lead to time waste spent on producing materials that don't lead to a sale and excess inventory. Similarly, waiting for raw materials, information, or processing time can cause delays and bottlenecks in the manufacturing process.
Prioritizing customer needs, recognizing waste, and working from the point of usage to the start of the production process, companies can minimize waste and enhance productivity. Incorporating automation technology, such as Makini's solutions, provides real-time insights into operations, aiding organizations in identifying areas of waste. Once identified, these wasteful activities can either be eliminated or minimized, leading to substantial improvements in productivity and cost savings.
Incorporating Makini integrations, such as those with Oracle Fusion Cloud Warehouse Management and Infor WMS, can be particularly beneficial. These integrations can streamline and optimize manufacturing processes by providing real-time data on inventory management, order fulfillment, and logistics. Automating and digitizing these processes can reduce waste forms such as excess inventory, overproduction, and inefficient resource use. Furthermore, these integrations can enhance visibility and control over the entire manufacturing supply chain, allowing for more precise demand forecasting and planning to further minimize waste.
In essence, whether it's through the lean methodology or innovative solutions like 3devo's machines or Makini's integrations, waste elimination is a crucial strategy in enhancing manufacturing productivity. It requires a shift in perspective, viewing waste not just as a byproduct of production, but as a potential resource that can be repurposed for value-adding activities.
3. Investing in Maintenance for Optimal Efficiency
Underpinning manufacturing efficiency is a robust maintenance strategy for machinery and equipment. A cornerstone of this strategy is preventive maintenance, a proactive approach aimed at addressing potential equipment issues before they escalate, thus mitigating the risk of unplanned downtime and its impact on productivity.
China Manufacturing Consultants (CMC) offers a comprehensive suite of services including assessments, observations, manufacturing consulting, and more. Their area of expertise spans lean manufacturing, new factory setup, NPI, APQP, manufacturing management, process improvement, maintenance, quality improvement, SPC, and others. They also consult on supply chain, ERP, factory management systems, HR, cost control, and delay reduction.
Preventive maintenance extends beyond simply avoiding unscheduled downtime. It involves creating a proactive system that enhances equipment lifespan, process control, and safety performance, making it one of the top success factors in high-performing manufacturing operations.
Comparatively, breakdown maintenance, a reactive approach taken post equipment failure, stands in stark contrast to preventive maintenance. With the advent of Industry 4.0, equipment complexity and technicality have grown, leading to multiple failure modes. Hence, without preventive maintenance, the essence of Industry 4.0 cannot be fully realized.
CMC champions the proactive approach to maintenance. They have crafted a roadmap for implementing a preventive maintenance system, which includes understanding the impact of poor maintenance, planning preventive actions, transitioning from reactive to preventive maintenance, maintaining total productive maintenance (TPM), and leveraging data via reliability-centered maintenance (RCM). Their proven expertise in this field has empowered businesses to reduce costs, increase productivity, and scale operations.
To further bolster this proactive approach, the Makini maintenance management integration can be utilized to prevent equipment failure by effectively managing and maintaining your equipment. The integration streamlines maintenance processes and keeps you abreast of equipment maintenance schedules. With Makini's solution, you can proactively schedule and track maintenance tasks, establish automated alerts and notifications for impending maintenance activities, and generate detailed reports on equipment performance and maintenance history.
Makini's website offers various use cases and integrations pertaining to maintenance. For instance, the 'Advanced Maintenance' use case and the Oracle Fusion Cloud Warehouse Management integration can be instrumental in supporting a proactive maintenance strategy. By leveraging the resources and tools provided by Makini, you can refine your maintenance practices and implement a proactive approach.
Makini also offers integrations for various warehouse management systems, including Oracle Fusion Cloud Warehouse Management and SAP Extended Warehouse Management. These integrations can boost productivity through Makini's maintenance management integration.
The preventive maintenance guide from CMC, complemented by Makini's integrated solutions, serves as a valuable resource for businesses. It provides insights into how a preventive maintenance system can reduce costs and increase productivity. CMC's offices in China and the US serve as consultation points for businesses looking to implement such systems and reap the benefits of a well-maintained manufacturing setup.
4. Streamlining Supplier Communications
Adopting advanced technologies is key to sustaining efficient operations. Missteps in communication can result in delayed material deliveries, disrupting the production timeline. An effective solution to this is Makini's universal API, a tool that enhances supplier communication, ensuring timely material delivery and smooth running of production processes. This method significantly boosts productivity by reducing delays and promoting adherence to production schedules.
For e-commerce businesses, there are numerous strategies for sourcing suppliers. Resources such as Alibaba, AliExpress, Indiamart, Thomasnet, and Maker's Row are incredibly useful. Having secondary suppliers can serve as a safeguard against any supply chain issues and backorders. Local shops without an e-commerce presence and international e-commerce store suppliers, particularly from countries like China and India, can also be potential suppliers. Initial conversations with potential suppliers should cover product availability, restocking frequency, delivery time, and payment conditions. Comprehending how dropshipping functions and considering dropshipping sites like Doba, SaleHoo, and Wholesale2b can be beneficial.
Supplier Relationship Management (SRM) is another critical component of the supplier communication process. SRM involves devising and implementing relationship strategies suited to each supplier type. The process entails supplier segmentation, where suppliers are categorized based on risk and profitability impact. The five categories of supplier segmentation are buy the market, ongoing suppliers, partnership suppliers, strategic alliance suppliers, and backward vertical integration suppliers. SRM is essential for evaluating supplier capability, measuring supplier performance, identifying and addressing challenges, forecasting, and staying updated about supplier innovations. Best practices for SRM include employing SRM software, appointing a supplier relationship manager, conducting supplier appraisals and reverse appraisals, implementing a supplier awards program, establishing win-win payment terms, and visiting key suppliers.
In terms of software solutions, the Vendr Intelligence Platform (VIP) features buyer guides, negotiation advisory, contract analysis, and integrations. VIP Pro includes everything in VIP, with additional features like intakes, approval workflows, renewal management, and supplier management. Platforms like these offer priceless resources and can significantly enhance supplier communication and management.
Makini's universal API provides a platform for integrating with different warehouse management systems, such as Oracle Fusion Cloud Warehouse Management and SAP Extended Warehouse Management. It facilitates communication between suppliers and the warehouse management systems, allowing suppliers to send and receive data related to inventory, orders, and shipments, ensuring seamless communication and collaboration. This integration enables businesses to automate manual processes, such as order placement and tracking, inventory management, and invoice processing. By streamlining supplier communication through Makini's API, businesses can reduce errors, improve efficiency, and enhance collaboration with their suppliers. Furthermore, Makini's API can provide businesses with access to valuable insights and analytics, allowing them to make data-driven decisions and optimize their supplier relationships.
5. Optimizing the Workplace Environment for Enhanced Productivity
A well-organized, safe, and efficient workspace is a critical factor in enhancing productivity. Leveraging advanced integrations like Makini can help organizations refine their workplace environment, ensuring optimal resource utilization and adherence to safety standards. This not only boosts productivity but also strengthens employee satisfaction and reduces accident risks.
Consider the transformational effect of a conducive workplace environment in the case of Cisco's Activity-Based Workplace. The organization's workplace resources team overhauled their strategy to maximize real estate investments and encourage employee collaboration. A significant part of this transformation was the adoption of Poly headsets, previously known as Plantronics Voyager headsets. These wireless devices allowed employees to stay connected to their phones irrespective of their workstations, fostering flexibility and mobility.
The outcome was remarkable. The new approach resulted in substantial real estate cost savings, increased employee collaboration, and improved job satisfaction. An additional 20 employees could be accommodated in a space that previously held only 21, indicating a 100% increase in occupancy. This shift also led to a yearly reduction of 16 tons of CO2 and a decrease in per-person space usage from 203 USF/person to 94 USF/person. The construction cost was $478 thousand, whereas the cost of implementing workplace strategy services was $28 thousand.
The Cisco case study underscores the potential of a well-optimized workplace environment in boosting productivity, enhancing employee satisfaction, and achieving cost savings. This is where Makini comes into play. By integrating Makini with warehouse management systems like Oracle Fusion Cloud Warehouse Management and Manhattan Associates, businesses can enhance visibility, track inventory accurately, and optimize workflows. This reduces the risk of accidents and improves overall safety.
Makini's real-time data synchronization enables better inventory management and accurate order fulfillment. Moreover, by automating routine tasks, Makini integrations can reduce manual errors and save time, thereby enhancing workplace efficiency.
In addition to warehouse management, Makini can also be used for general workplace optimization. Businesses can leverage its features to streamline processes and workflows in various areas such as project management, document collaboration, and task automation. This can significantly contribute to enhanced productivity and optimized operations.
In conclusion, investing in advanced integrations and strategies like Makini can help organizations create a workplace that is efficient, safe, and conducive to high productivity.
6. Strategies to Reduce Manufacturing Waste and Costs
Emphasizing the importance of reducing waste and costs to boost productivity in the manufacturing sector is paramount. One such illustration is the transformation initiated by China Manufacturing Consultants (CMC) in a Chinese factory, where they realized substantial cost savings without resorting to automation. This initiative was primarily driven by a thorough identification and reduction of waste areas like overproduction, waiting time, transportation, over-processing, inventory, motion, and defects.
CMC coordinated with the factory's senior management to set up lean-style manufacturing lines, culminating in a reorganization of the assembly line. Such reengineering led to a quality improvement and a decrease in rework, subsequently reducing the number of production operators from 208 to 123. Additionally, administrative support processes were streamlined, leading to the reduction of 38 indirect workers.
One distinctive element of this transformation was the incorporation of hands-on training programs for managers and operators. These programs were centered around critical areas like lean training, preventive maintenance, material control, 5S, standard work, quick changeovers, and quality alerts development. Over a 12-month engagement, these measures resulted in a significant cost reduction of 15 million USD per year.
Furthermore, inventory control was significantly optimized, leading to considerable savings. The factory's increased capacity enabled it to take on new business opportunities, resulting in an additional profit of 15 million USD.
In a similar vein, Macrofab, an electronics manufacturing platform, used similar principles to assist a Texas-based energy company in overcoming challenges associated with offshore manufacturing. The energy company was struggling with supply chain delays, lack of transparency, and communication issues. Macrofab intervened to simplify the manufacturing journey, offering real-time order tracking and selecting ideal manufacturing facilities.
As a result, the energy company observed a significant reduction in inventory costs, quicker iteration times, and improved visibility into order fulfillment. The iteration time fell from three months to seven weeks, including delivery.
These case studies highlight the effectiveness of leveraging integrations, such as those provided by Makini, to gain real-time insights into operations. Makini provides integrations with various warehouse management systems, including Oracle Fusion Cloud Warehouse Management and Manhattan Associates Warehouse Management IBM. These integrations can be utilized in manufacturing to pinpoint areas of waste. By connecting the manufacturing process with the warehouse management systems, Makini helps track and analyze data related to inventory levels, production efficiency, and resource allocation. This data can shed light on areas where waste may be occurring, such as excess inventory, production bottlenecks, or inefficient resource utilization. With real-time insights, manufacturers can make data-driven decisions to optimize their operations, reduce waste, and improve overall efficiency.
The utilization of Makini's integrations can also help improve transportation efficiency in manufacturing. By seamlessly connecting with these systems, Makini empowers manufacturers to automate and optimize transportation processes, resulting in improved efficiency, reduced costs, and better overall supply chain management.
Moreover, Makini's integrations can help reduce over-processing in manufacturing by streamlining the warehouse management process. By integrating with these systems, manufacturers can automate various tasks such as inventory management, order fulfillment, and shipping. This reduces the need for manual intervention and minimizes the risk of errors and inefficiencies. Makini's integrations enable manufacturers to optimize their manufacturing processes and improve overall operational efficiency.
7. Implementing Efficient Inventory Management Practices
Mastering inventory management is a critical aspect of elevating productivity in the manufacturing sphere. It serves as a balancing act between overstocking, which elevates costs, and understocking, which can cause production delays. A prime example of this is the educational firm, Curriculum Associates, which supplies print materials and software to educators and learners throughout North America. Due to a rapid annual growth rate of 40%, the company had to extend its operational scope and invest in a new automated distribution system.
With the aid of Bastian Consulting, a facility sizing study was conducted to determine the necessary size for the new distribution center. The study's outcome led to the consolidation of two smaller facilities into a single distribution center, resulting in a 167% increase in capacity to manage order volume. This consolidation allowed Curriculum Associates to dispatch over 16 million units each day. The project also included the successful integration of a new material handling system and warehouse management system (WMS), all monitored meticulously by Bastian Consulting.
Yet, the consolidation of inventory management systems remains incomplete without the implementation of a tool like Fishbowl. Fishbowl offers real-time inventory management across all locations and integrates with other key business functions to automate processes. It helps manage simple to complex manufacturing processes and provides robust order fulfillment for stored inventory. This includes features like inventory tracking and warehouse operations management.
An illustrative case is KidWind, an educational project that utilized Fishbowl Manufacturing to enhance inventory tracking and standardize operations. Before Fishbowl, KidWind relied on handwritten notes for inventory tracking, which resulted in organizational disarray and inaccuracies. With Fishbowl's implementation, the project underwent a transformation, improving staff relationships and reducing on-hand inventory costs from $270,000 to a range of $80,000 to $100,000.
However, it's crucial to highlight that advanced systems like Makini also play a significant role in ensuring optimal inventory management. Makini provides solutions that help organizations improve their inventory management processes and streamline their operations. Among its features are inventory optimization and integration with Oracle Fusion Cloud warehouse management. Implementing advanced systems like Makini and Fishbowl can ensure that organizations maintain the right amount of inventory at the right time, thereby preventing overstocking and understocking. This can considerably enhance productivity and reduce inventory costs, contributing to optimized operational performance.
Conclusion
The main points discussed in this article revolve around the importance of refining the material ordering process, reducing waste and costs, optimizing the workplace environment, investing in maintenance, and streamlining supplier communications. These strategies are crucial for enhancing productivity in the manufacturing industry.
Efficient inventory management is a key factor in improving productivity. By implementing tools like Fishbowl and advanced systems like Makini, organizations can optimize their inventory levels, prevent overstocking or understocking, and improve overall operational performance. This leads to cost savings, streamlined operations, and uninterrupted production processes.
Furthermore, reducing waste and costs through strategies such as lean methodology and preventive maintenance can significantly enhance productivity. By identifying and eliminating non-value-adding activities and implementing proactive maintenance measures, businesses can streamline their processes, reduce downtime, and improve resource utilization.
Creating a conducive workplace environment is also essential for enhancing productivity. Integrations like Makini can help organizations optimize their workplace by providing real-time insights into operations, streamlining workflows, and ensuring adherence to safety standards.
In conclusion, implementing efficient inventory management practices, reducing waste and costs, optimizing the workplace environment, investing in maintenance, and streamlining supplier communications are all crucial strategies for enhancing productivity in the manufacturing industry. By adopting these practices and leveraging advanced tools like Makini, businesses can achieve cost savings, streamline operations, and ensure optimal resource utilization.
Enhance your organization's productivity through efficient inventory management practices with https://makini.io/.